更新日:2024.10.31
電機メーカー A社様
- 創業:約60年
- 製造品目:電子製品、電装品
- 従業員数:約300人
- 本社及び関連出資企業2社
課題解決のポイント
-
100台以上の設備ごとにメンテナンス内容・時期が異なり抜け漏れ発生
保全情報は紙帳票で記録、エクセルに再入力している
部品の出庫履歴/残数管理は現場でメモし、事務員が事務所で情報を書き換え
-
「設備保全DX」で各設備のメンテナンス予定・項目を一元管理
保全結果、修理後の報告書作成、承認・回覧のワークフローを電子化
各種部品・部材をシステムで一元管理、使用時は現場で即時入力
-
予定と点検項目のシステム化により、月間保全作業時間を40%削減
エクセル再入力の時間が大幅減。月間で40時間の短縮となる
部品の出庫数、残数をリアルタイムで把握。発注漏れがゼロに。
NAVINECTの導入を決めた理由
点検フォーム・物品管理・異常報告のワークフロー が全て揃っている
弊社は設備保有数も多く、設備ごとにメンテナンスの項目や実施時期もまちまちで、属人化、アナログ管理での限界を感じていました。何らかのシステムを探してはいたのですが、保全と一口に言っても業務内容はさまざま。部分最適な各社のソフトを複数使うことになるのかな、かえって手間になりかねないな・・・と思っていたところ、NAVINECTの設備保全DXを見つけました。 「定常的、定形的な業務に適した入力フォーム」「部品、消耗品などの管理」「有事の際や、非定型業務にも運用できる入力フォーム」など、一つの製品画面に必要な機能を揃えられることが分かり、初期・運用のコストや習熟までの工数が削減できることから、本製品の導入を決めました。
導入効果
【導入前】
・100台強の設備を保有。点検の周期も項目も異なり、管理しきれない
保有設備の数≒点検記録用紙の種類 という状態でした。ここに点検周期の違いや担当者の情報などが絡んできます。管理・集計業務も設備の大まかな系統ごとに複数担当者を設けて負荷分散していましたが、作業の抜け漏れや担当ごとに管理方法、集計方法が異なるなどの問題がありました
・有事・修理の際は紙報告書を作成→事務担当者がエクセルに再入力
何らかの修理・交換などを実施した際には、上記の点検記録とは別途の報告書を点検作業者が紙で作成、これを事務担当者がエクセルに再入力していました。フォーマットはあるものの入力規則はあったり無かったり。再入力はもちろん前段階の照合作業にも時間を割かれていました。
・点検に使用する部品、部材管理も同様。紙でメモ→事務担当がエクセル再入力
保全にまつわる部品管理についてもアナログ管理で、起点は点検作業担当者の紙のメモ。同一部品を使っているのに、AさんとBさんとではアイテム名称が異なるなど、上記と同様に再入力と照合作業が負荷になっていました。
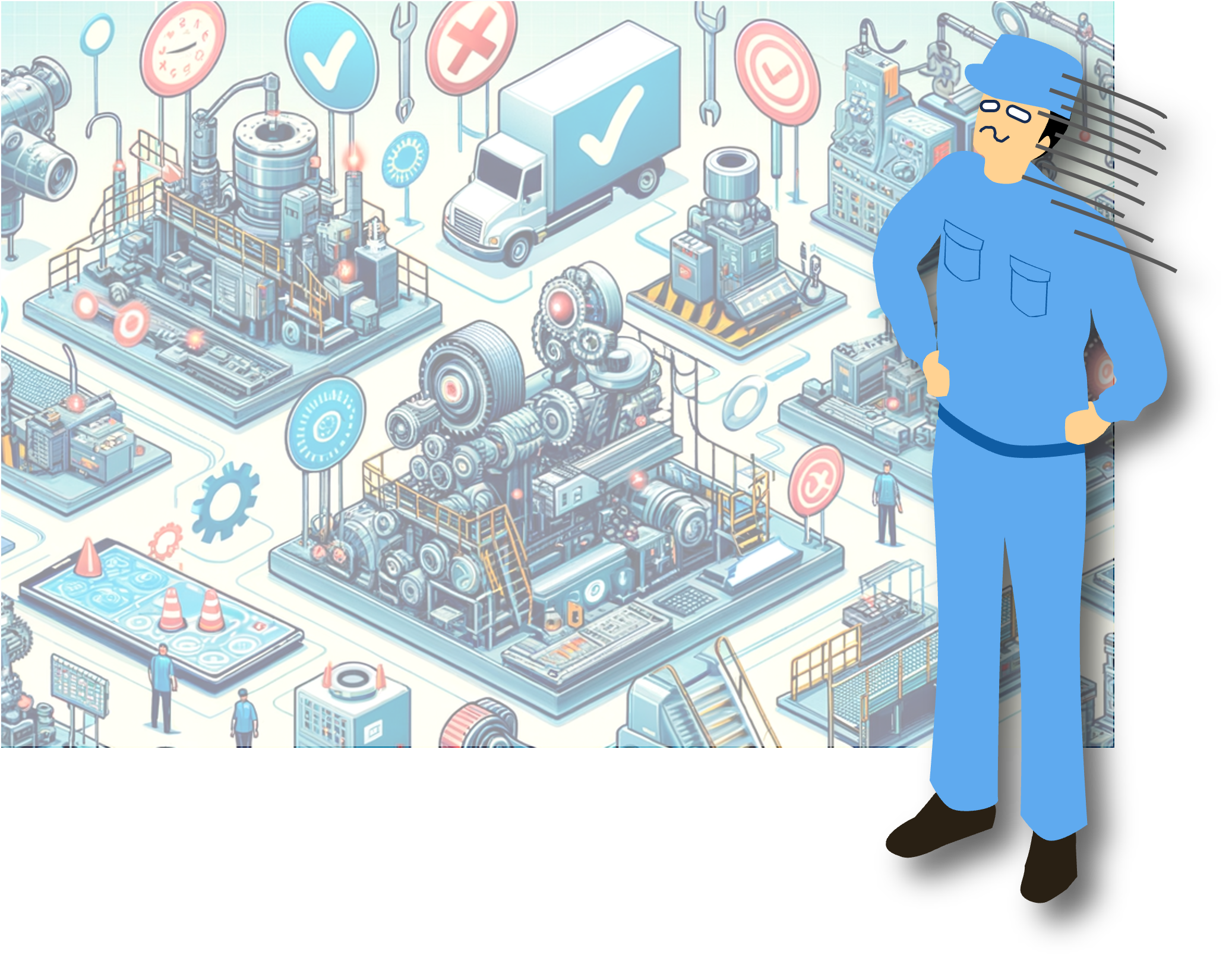
【導入後】
・点検表を体系的に分類、入力規則の設定や予定の明瞭化でミスロス削減
設備ごとの点検表は「工程管理」のメニューで作成しました。「工程>機械>作業種別>カテゴリ>入力項目」と、帳票を管理する体系・親子関係の構造があらかじめあるので、この関係性に沿って点検表を分類して作成。体系化できたことで予定も立てやすく、作業する側も把握しやすくなりました。予定に対する実行履歴も確認ができ、抜け漏れは激減。新しい資産が増える際などもスムーズに分類ができています。
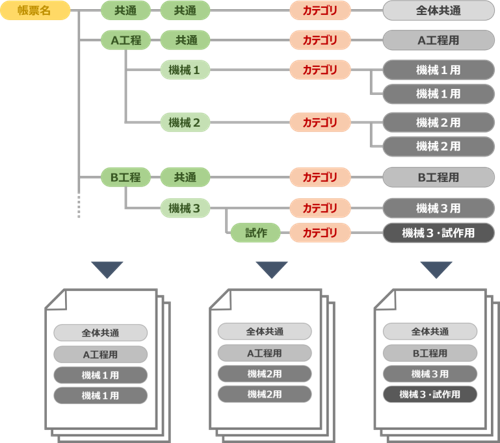
入力規則も種類が豊富で、集計を意識しながら適したものを配置。入力のミスが減り、主要な集計はほぼシステム内で完結。この集計とその後の共有に要す時間も大きく削減できました。例外は月に一度レポート用にエクセルでダウンロードして加工する程度です。 担当者ごとによく使う帳票、全く使わない帳票があるので、お気に入りや直近使ったものをすぐに呼び出せる機能も重宝しているようです。
・異常や修理など詳細な記載が要るものもデジタル化
点検作業ほど頻度は高くないものの、異常やその後の修理の際には具体的な文章記載を用いて運用しています。ここでは「帳票管理」のメニューを使い、紙の記録用紙に似せたフォーマットを画面に作って使用しています。この報告書の各項目にもそれぞれ個別の入力規則を設けることができるので、定量的なものはもちろん、定性的な項目の頻度を集計してカイゼンに活かそうとしています。写真も残せるので、異常箇所の撮影→後日の修理の際に参照しています。
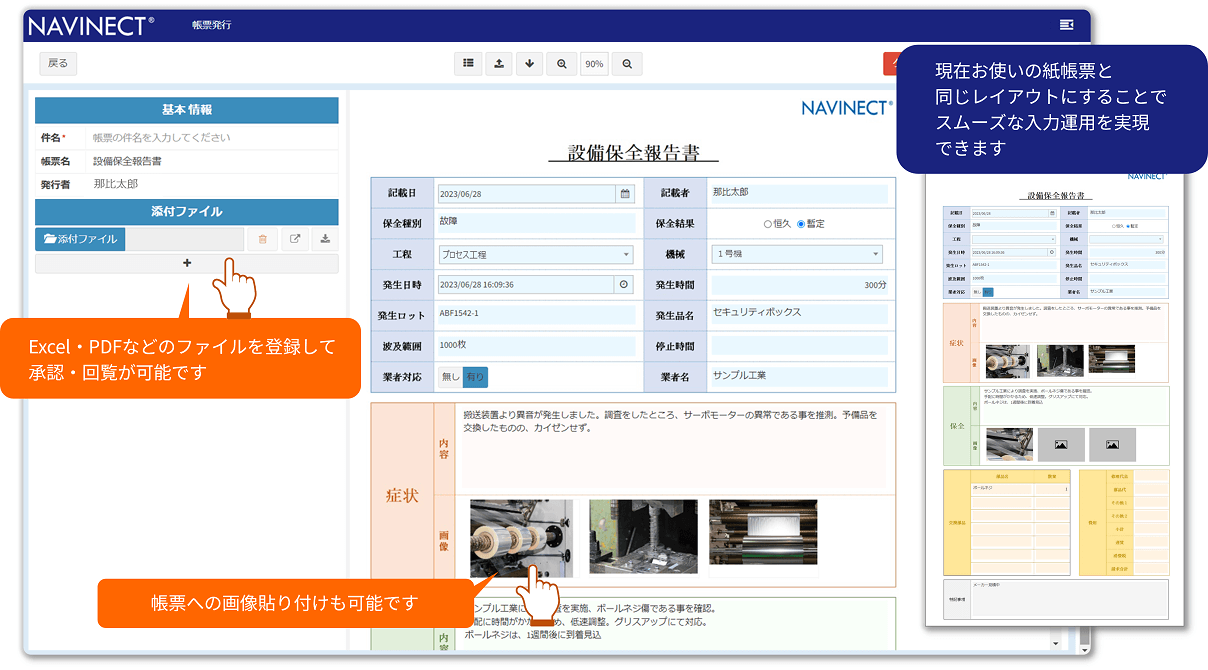
・コトと合わせてモノも管理。メンテナンス資材や部品も一元化。
計測機や工具など、使ったら元に戻すものの所在がとても明瞭になりました。今使っている人や最後に誰が使ったかが分かるのがポイントですね。また、油・フィルター・ネジなど使うと減るものがあります。弊社では後者も管理したかったので、数量管理を行っています。「複数部門で同じ物品を買ってしまい、工場全体で見ると過剰な仕入れをしていた」などがありましたが、この「在庫管理」のメニューで一元化することができ効率的な発注につなげられています。

ご担当者さまの声
システムの導入から概ね半年強が経ち、上記のような当初から見えていた課題解決の他にも、集計・見える化することで新たにカイゼンの糸口が見つかったケースも出てきました。例えば「設備分類ごとだけでなく課ごとの保全対応時間の集計」を見てみると、いくつかの課が平均よりも短い時間でタスクをこなせていることが分かりました。詳しく聞いてみると「状況によりその後の動きが分岐するポイントについてあらかじめそのパターンをメモにしておき、それを見ながら点検していた」などの工夫を行っていました。このあたりはこのソフトウエアですぐに応用できますので、適用可能な設備や組織から水平展開することができました。 また「設備保全DX」は機能が豊富なので、例えば場内の管理事務・総務関連業務など用途を広げた活用にも着手を始めています。
NAVINECT導入担当より
設備保全DXの王道のような使い方と評価をいただき大変光栄です。本製品に限らず、NAVINECTは汎用性や“つながる”が特徴ですので、ご記載のようにさまざまな用途に応用できます。こんな使い方はできそうか?などのお問い合わせがございましたら引き続きご連絡いただけたらと思います。
-
「設備保全DX」を知る