更新日:2025.3.13
精密機器メーカー A社様
- 創業:約70年
- 製造品目:精密機器・部品製造
- 従業員数:約1,000人
課題解決のポイント
-
3σをはじめとしたSPC(統計的工程管理)を行いたいが、各種検査結果のデータが一元管理できておらず実現に至っていない。
検査結果異常の際、上長にタイムリーに報告を行いたいが、検査担当者により
報告基準やタイミングが異なる。報告すべきか悩むことも多い。 -
検査機や測定機のデータは直接DBへ、ヒトによる検査データはフォーム入力を
通じて登録することで一元管理化。各種管理図や統計量を同一のソフトで
閲覧・承認できるシステムを導入。検査異常となる条件を検査項目ごとに設定。条件を満たした場合に
職制・管理職に自動でメール連絡を行う仕組みも導入。 -
属人化が解消、データの整合性やアクセス性が向上。重複や誤入力も減少。
分析やトレンド把握もスムーズになり、意思決定が迅速化。タイムリーに情報が入るため即時に対処でき、管理者は遠隔でも指示対応が
可能に。正確なデータ履歴が残ることにより分析と対策の精度が向上。
導入効果
【導入前】
・3σをはじめとしたSPC(統計的工程管理)を行いたいが、
各種検査結果のデータが一元管理できておらず実現に至っていない。
品質管理を目的とした各検査データには大きく2種類あり、検査機や測定機など機械が自動的に取得するものと、検査員が手動で収集するものがあります。それぞれの検査結果データ、特にヒトの手によるものは個別のエクセルファイルに保存されていました。 データが分散化しているため、集計や統計処理を行うのも手間でした。自ずと限られた社員にしか扱えない状況、属人化が進んでいました。エクセルを使った検査結果の入力にはいわゆる「表記ゆれ」なども存在しており、データの記録や管理の方法を統一しきれないという課題もありました。
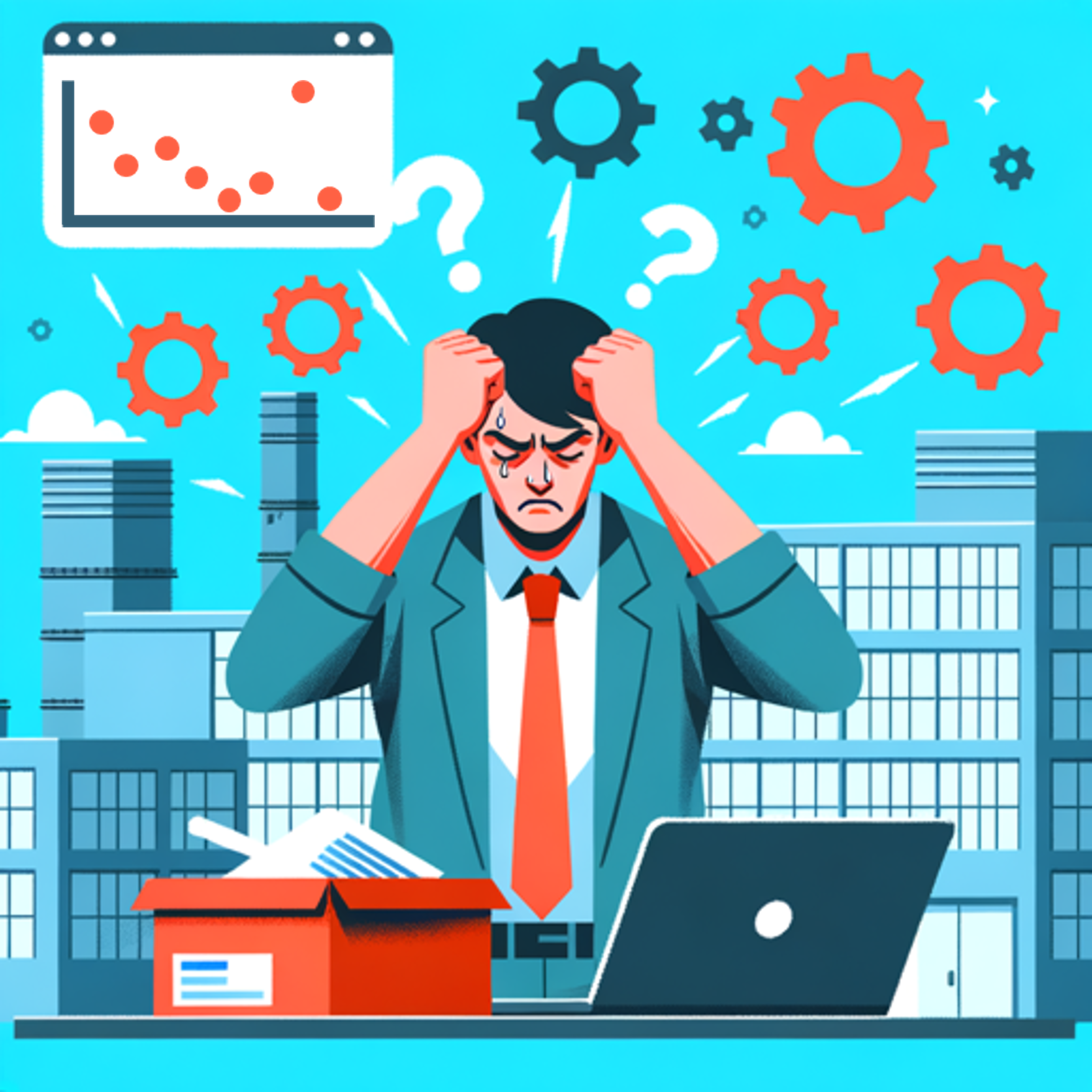
品質基準の見直しの際には過去の実績や履歴を参照することになりますが、ここでも大きな手間がかかります。必要なデータを素早く見つけ出すことが難しく、意思決定に必要な情報へのアクセスが遅れ、対応スピードが遅くなっていました。 他にも、データを統合して分析する際に各ファイルを手動で開いて確認する必要があり、時間がかかるだけでなく、ヒューマンエラーのリスクも高まります。ファイル間でフォーマットが異なる場合は、データを一貫した形で分析するための前処理が必要となり、分析プロセスが複雑化します。また担当者が異なる場合には各ファイルの内容理解に差が生じることもあり、組織全体でのデータ共有が難しい状況でした。
・検査結果異常の際、上長にタイムリーに報告を行いたいが、検査担当者により
報告基準やタイミングが異なる。報告すべきか悩むことも多い。
検査結果に異常兆候が見られた場合に、どのタイミングで報告するべきか不明確な項目や、基準が統一できていないものもありました。検査担当者によっては報告の必要性やタイミングについて悩むことも多く、結果として報告が遅れる、または見逃されるリスクが生じていました。異常発生の際、速やかに適切な対応をとることができなければ、製品の品質保証に影響を及ぼし、不良品の流出を引き起こす可能性もあります。 報告の属人化が進んだ場合、対応の一貫性が失われ問題の再発防止策が十分に機能しない懸念もありました。
【導入後】
・属人化が解消、データの整合性やアクセス性が向上。重複や誤入力も減少。
分析やトレンド把握もスムーズになり、意思決定が迅速化。
検査機や測定機からのデータを直接データベース(DB)に一元登録し、ヒトによる検査データもフォーム入力を通じて統一的に管理できる仕組みを導入しました。
まず、データの一元管理により属人化が解消されます。従来は、異なる担当者がそれぞれの方法でデータを管理していたため、データの収集や整合性にばらつきが生じていました。DBへの一元登録により、すべてのデータが統一的に保存されるため、担当者が変わってもデータ管理の方法が統一され、データの正確性と一貫性が保たれます。
「品質管理(SPC管理)」を使うことで、データへのアクセスを効率化、分析・集計・統計処理も自動化できました。すべての検査データが同じDBに格納されることで、必要な情報をUI画面を通じて迅速に検索・抽出・計算することが容易になっています。これにより、問題またはその兆候の早期発見や素早い意思決定が可能となり、業務効率が向上しています。
作業員による検査結果データの入力は、「工程管理」で検査種別ごとのフォームを用いて入力、重複や誤入力を減らし、入力規則を設けることで精度が向上。扱いやすいデータを登録できています。
これらの一元管理と正確なデータのおかげで品質管理の精度とスピードが向上しました。出力を意識して設定した項目にデータを入力することにより、品質の傾向を把握するための分析や改善の基礎がより強固になり、製品の品質をより高い水準で維持することができるようになりました。
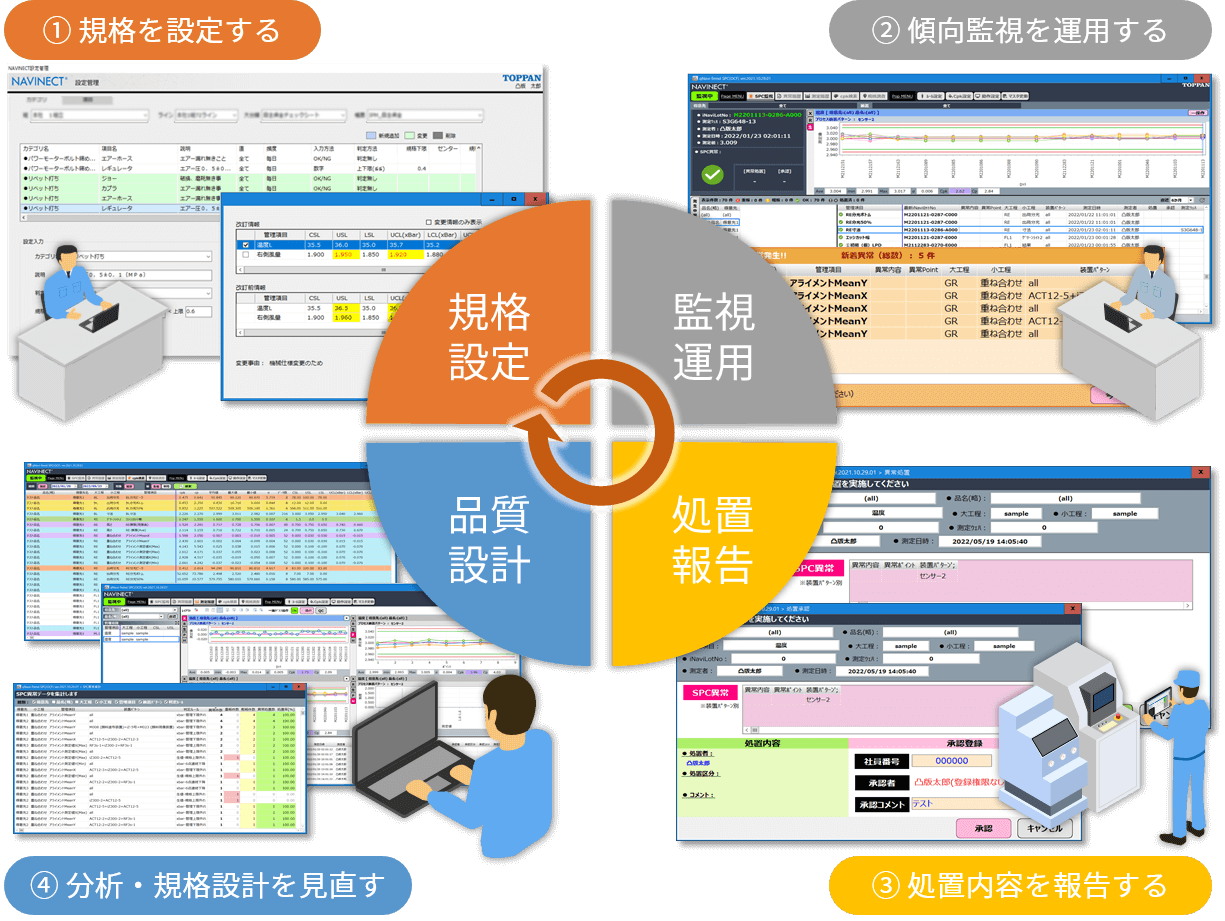
一元登録されたデータを基に、管理図や統計量を統合的に閲覧・承認できるシステムを導入したことにより、以下のような効果が得られています。
まず、データの分散化が解消されることで、過去のデータ参照が容易になります。従来は各検査種別ごとに分かれたエクセルファイルを手動で検索する必要がありましたが、「品質管理(SPC管理)」パッケージでは一つのソフト内で全てのデータにアクセスできるため、必要な情報を迅速に取得できます。データの確認や問題の原因探索が効率化、意思決定のスピードも向上しました。
また、同一のソフトで各種管理図・統計量を閲覧できるため、データ分析やトレンドの把握がスムーズになります。これらが一元的に表示されることで、品質の変動やパターンを直感的に理解でき、品質管理の精度が向上します。異常値やトレンドの変化は期間、検査項目、製造品種など層別でも確認できるため、的を絞った対策も講じやすくなります。
さらに、プロセス改善のためのヒントも得やすくなりました。統合されたデータから得られる全体的な視点を持つことで、改善すべき領域や優先度をつけやすくなしました。経験や勘への依存度が減り、データドリブンのアプローチでプロセス改善を進める土台ができたことで、組織全体のパフォーマンス向上に寄与できると思っています。
システム内でのデータ閲覧や承認のプロセスにルールを設けることもできるので、データの整合性が保たれるだけでなく、必要な承認フローをスムーズに進めることも可能になりました。
・タイムリーに情報が入るため即時に対処でき、管理者は遠隔でも指示対応が
可能に。正確なデータ履歴が残ることにより分析と対策の精度が向上。
「SPC管理」で異常判定の条件を検査項目ごとに設定し、条件を満たした場合に「通知・監視レポート」を用いて自動でメール連絡が行われる仕組みを導入することで、以下のような利点がもたらされています。
まずは、報告・エスカレーションのタイミングや基準が統一されました。検査担当者はそれぞれ異なる報告基準を持つこともあり、異常兆候の発見時に報告するか否か迷ってしまう場合がありました。今回導入した異常判定の条件設定と自動通知により、報告基準のばらつきが解消されています。
また自動通知機能により、異常が発生すると速やかに関係者に情報が伝達されます。これにより、見逃しや報告の遅れが発生するリスクが大幅に低減され、問題への素早い対処が可能になります。特に、重大な異常が発生した場合には即時対応が求められるため、この自動化により対応のスピードが大幅に向上し、製造ラインが止まるなどのロスも減らすことができました。
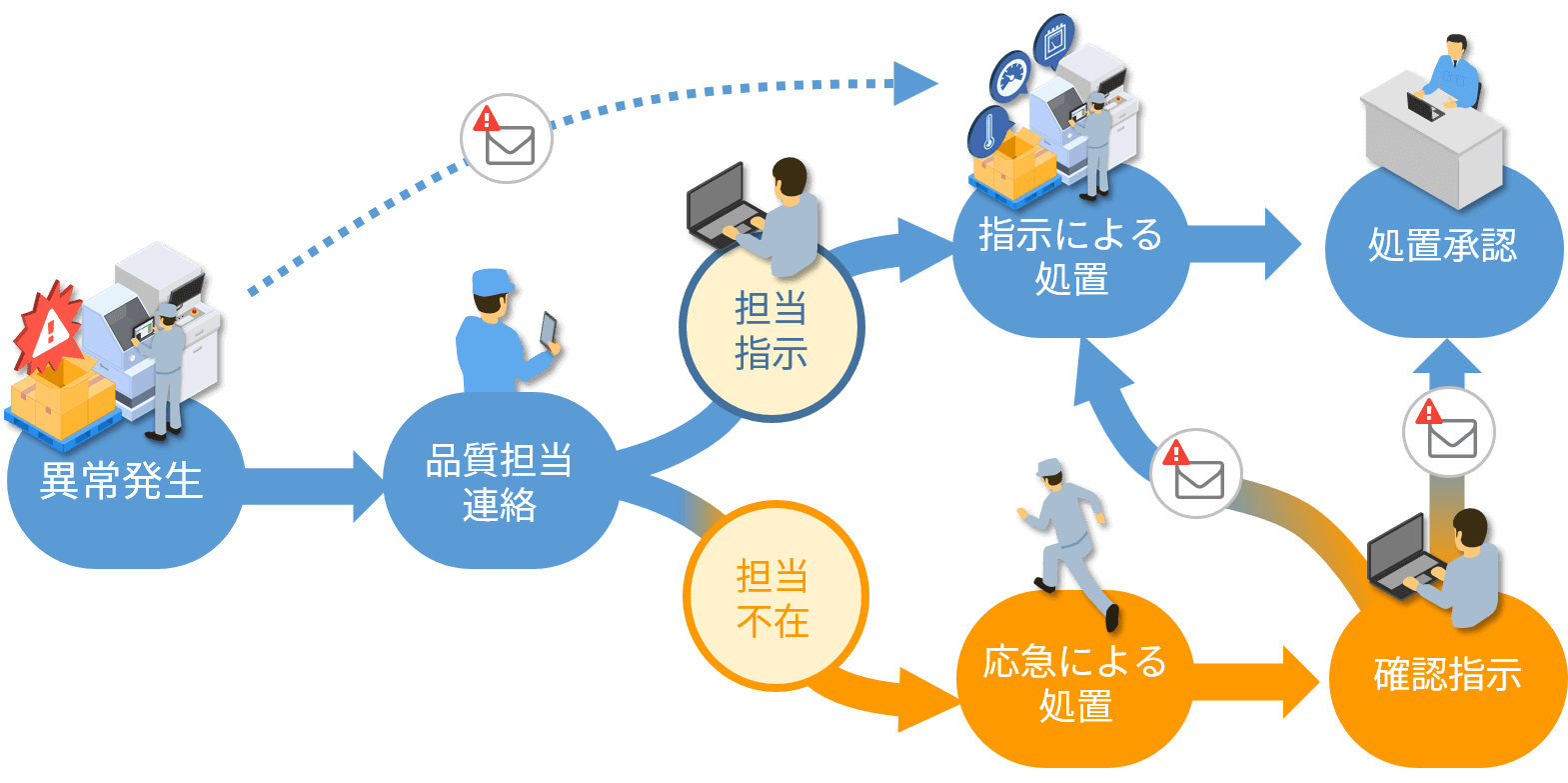
さらに、報告の遅れによるリスクが軽減されることで品質の安定化にもつながっています。異常への素早い対応は製品品質の維持や顧客満足度の向上につながりますので、組織の信頼性を高められるものと思っています。また、異常の発生頻度や傾向をデータとして蓄積することで、さらなる品質改善のための足掛かりを得られ、基準の見直しを合理的に行えるようになりました。
この仕組みにより、報告プロセスの透明性とトレーサビリティも向上しました。報告が自動的に記録されるため、どの異常がいつ報告され、どのように対応されたかを容易に追跡できます。内部監査やコンプライアンス活動にも寄与できるものになりそうです。
-
「品質管理」を知る
-
「工程管理」を知る
-
「通知・監視」を知る