更新日:2022.11.24
製造デジタルトランスフォーメーション(DX)の進めかた【前編】では、挫折を避けるためのヒントや、どこからDXを始めるのか、その基盤づくりについてご紹介しました。【後編】では具体的に成果を上げ、真のDXを実現するために必要なことや考え方についてご紹介します。 製造デジタルトランスフォーメーション(DX)の進めかた【前編】はこちらから >
導入ステップの具体例 Part2
真のDX実現へ向けて
STEP 5「進捗管理」の効率化
生産性を高めるためには、人材や設備、時間などの資源を効率よく、最小限に使用する必要があります。しかし、何を・どれくらい・いつまでに生産するのか、そして現在の進捗はどうなっているのか、の全体像を人の手で把握することは、容易ではありません。この難しい進捗管理を助けてくれるのがMES:Manufacturing Execution Systemと呼ばれるものです。全体的な生産計画をつかさどるERPと、SCADAとの間で機能し、設備の前準備・条件設定から実績収集までの製造現場全体の進捗を可視化し、管理を容易にします。生産性向上をデジタルの力で実現するためのキーとなるのが、MESです。
NAVINECTエッジ「製造管理(MES)」パッケージを知る >>
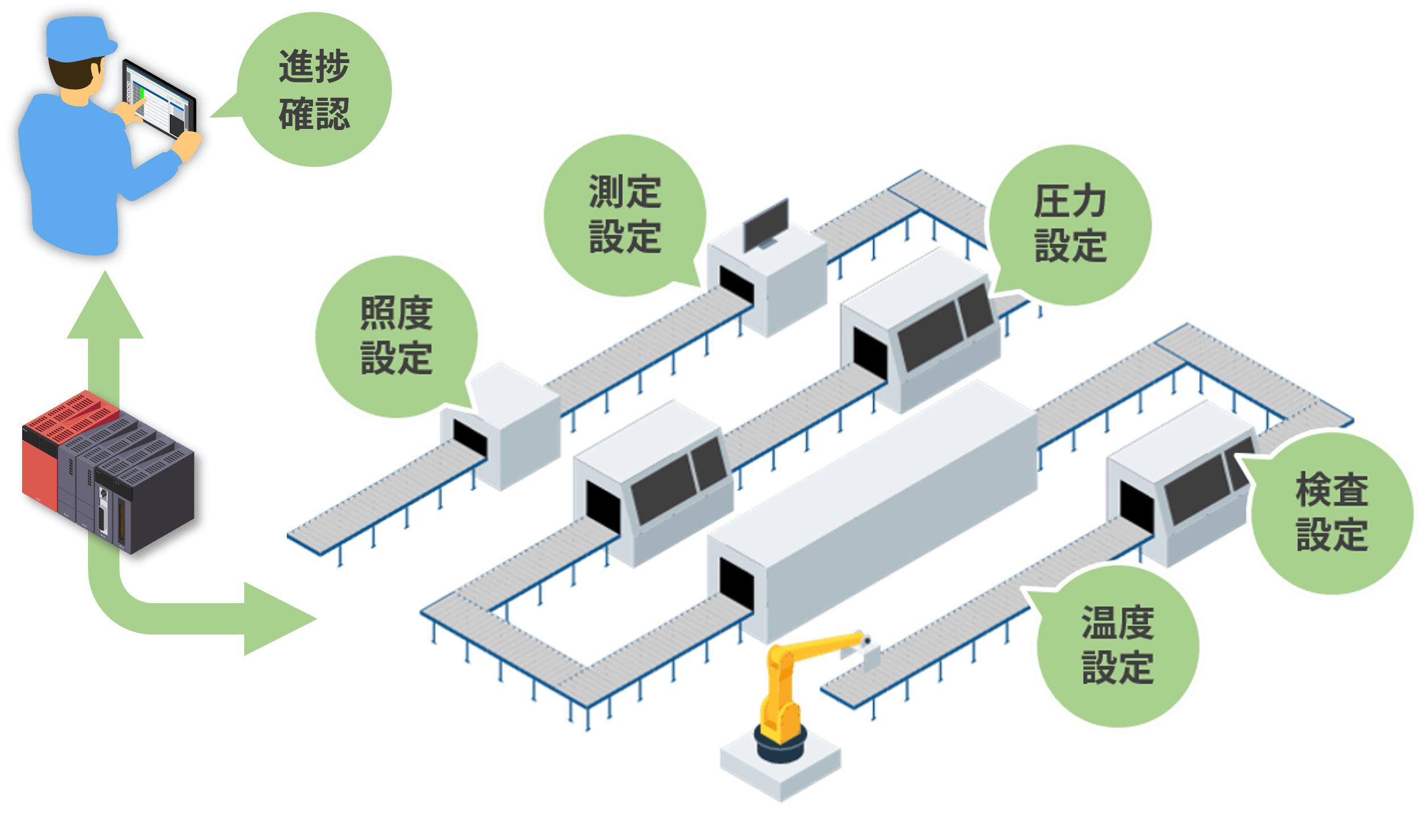
- MES
- SCADA
- 設備設定自動化
- 誤投入防止
STEP 6「生産状況」の監視・異常予防
効率化が求められるなかで、生産を止めないために異常をいち早く発見したい…そのためにヒトが何度も現場を巡回しているケースもあるかと思います。しかしヒトによる巡回では、異常発見の遅れが情報共有の遅れにつながり、それが対策の遅れにつながるほか、情報共有もヒトの手で行うのでは、異常の再発防止対策もままならないことになってしまいます。
このような事態を避けるために、装置の状態を遠隔から集中管理を行うことで、異常の発生は即時に把握できるのが望ましい形です。作業者も巡回に時間を割かれることもなく本来の生産活動に打ち込むことができます。
NAVINECTエッジ 「生産監視」パッケージを知る >>
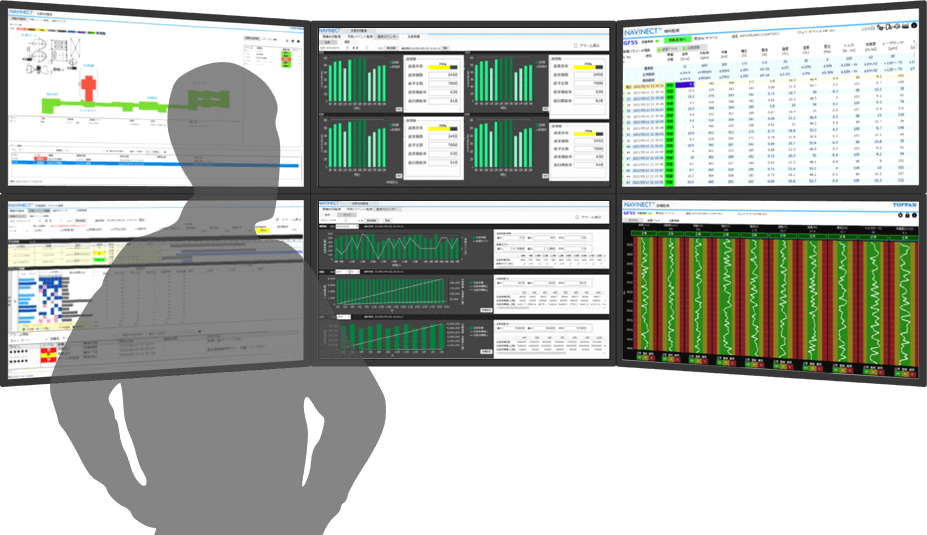
- 集中監視
- リアルタイム
- 予実管理
- スループット改善
STEP 7「ヒト」が活きる現場づくり
製造現場の自動化が進んだと言っても、まだまだヒトが果たす役割は多く、むしろ現場がスリム化されたぶん、その管理の重要性は高まっていると言えます。また労働人口の減少が止まらないなか、技能の伝承も産業全体の課題となっています。さらにコロナ禍によって作業者の健康管理の必要性もあらためて見直されています。
勤怠、教育、安全衛生、配置など、人的リソースを管理するシステムは以前より個別に存在してはいるものの、個人に紐づいて連動したものではありませんでした。これらの情報を一元管理できることが、人的リソースを最大限に活用し、さらに働きやすい職場を作るうえで必要な要素の1つとなっています。
NAVINECTエッジ 「作業者管理」パッケージを知る >>
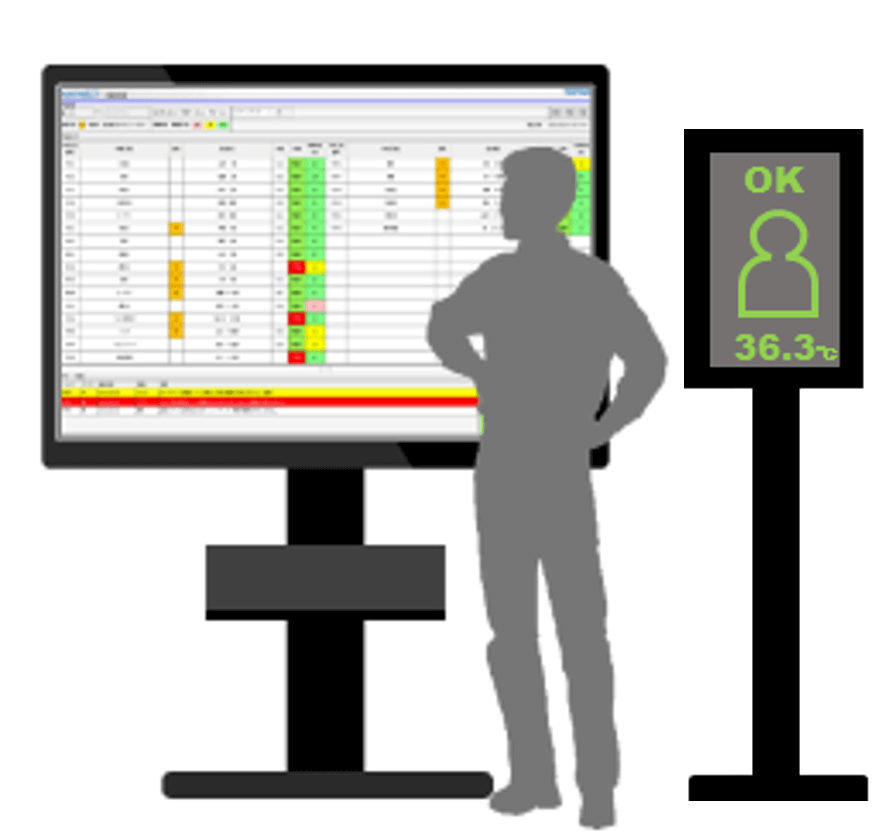
- 健康経営
- 技能伝承
- 安全衛生
- 事業継続
STEP 8「データインテグリティ」の実現
すべての生産活動はお客さまからの信頼の上に成り立っています。信頼を獲得するためには、何がどうつくられたかのトレーサビリティはもちろんのこと、昨今ではその根拠となるデータが噓偽りなく確かなものであるか”データインテグリティ”が非常に重要になっています。
規格設定から監視運用、処置報告、品質設計までの一連のワークフローをデジタル化することによって、変更履歴や改ざんの有無の確認が可能になり、データインテグリティの担保につながります。
NAVINECTエッジ「品質管理」パッケージを知る >>
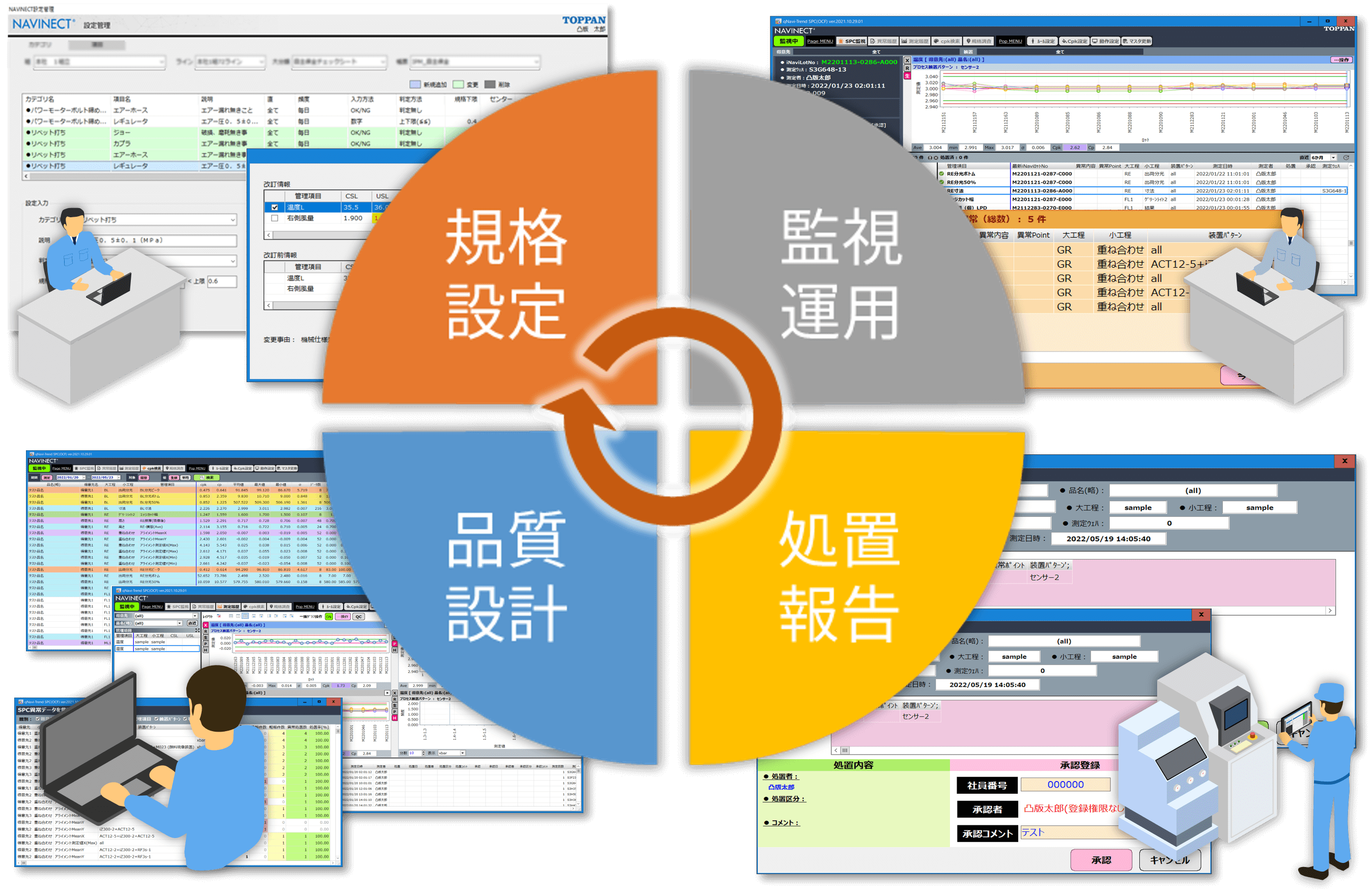
- 保全報告
- 試作指示
- 作業指示
- 廃棄指示
製造DXへの道のりは一足飛びという訳にはいかず、困難も多いもの。目的を見据えて、根気強く、継続的な取組みが必要です。「NAVINECT」はお客さまが着実にステップを刻めるよう多彩なサービス・ソリューションを用意しています。何から手を付けたら良いかわからない、なかなか効果が実感できない、とお悩みのお客さまはぜひお気軽にご相談ください。
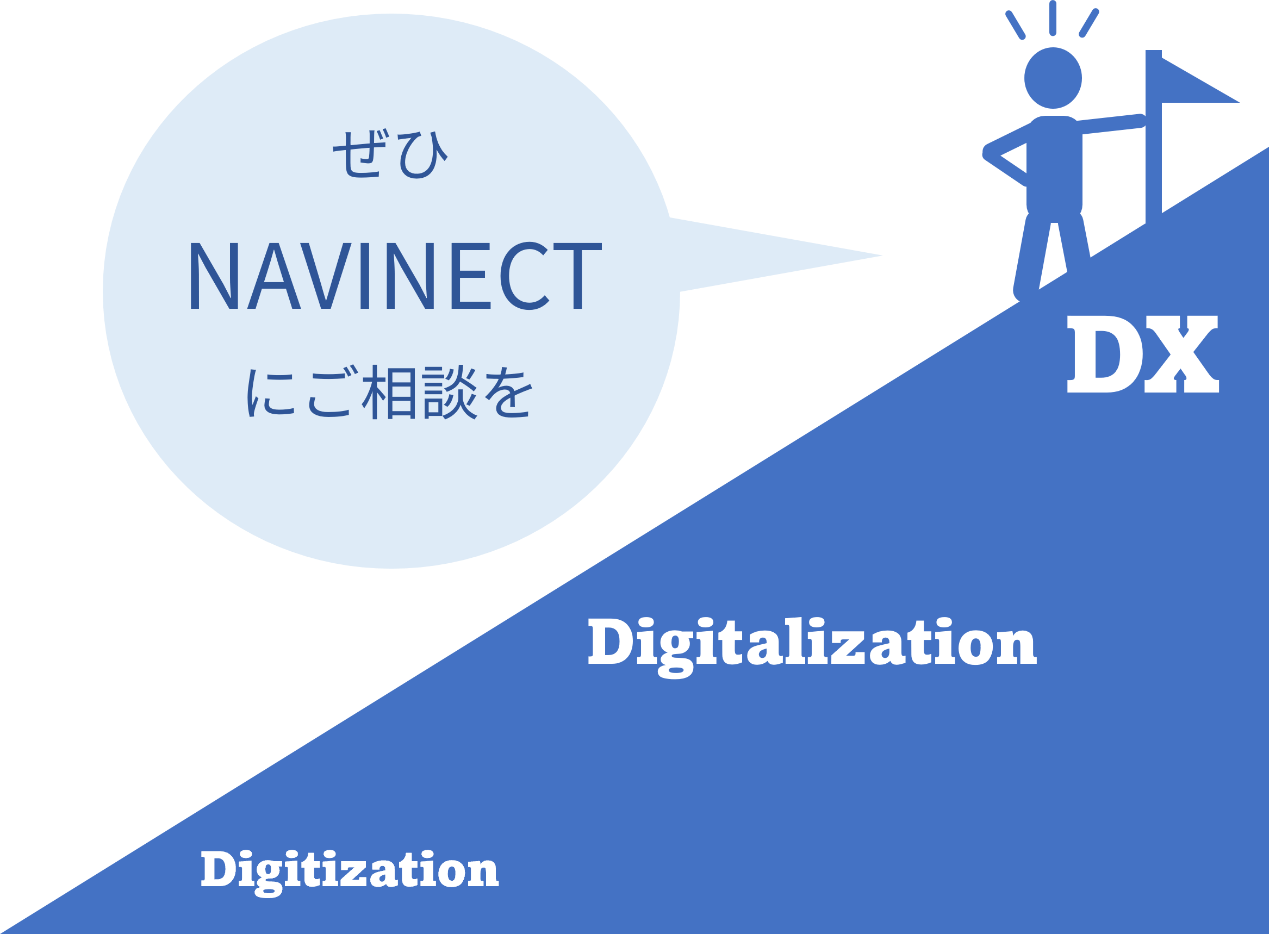
-
NAVINECTの特徴を知る
-
NAVINECT製品を知る