更新日:2023.10.5
株式会社上村エンタープライズ様は、「“思い”を“カタチ”に変えるオーダーメイドカンパニー」をスローガンに、3Dの技術と微細加工の技術を活かして顧客企業の期待に沿った樹脂製品の製造、精密機器の加工をオーダーメイドで受託している企業です。 今回はNAVINECTとRFIDを活用した工程の見える化について、上村社長にお話を伺いました。 上村エンタープライズ様HPはこちら
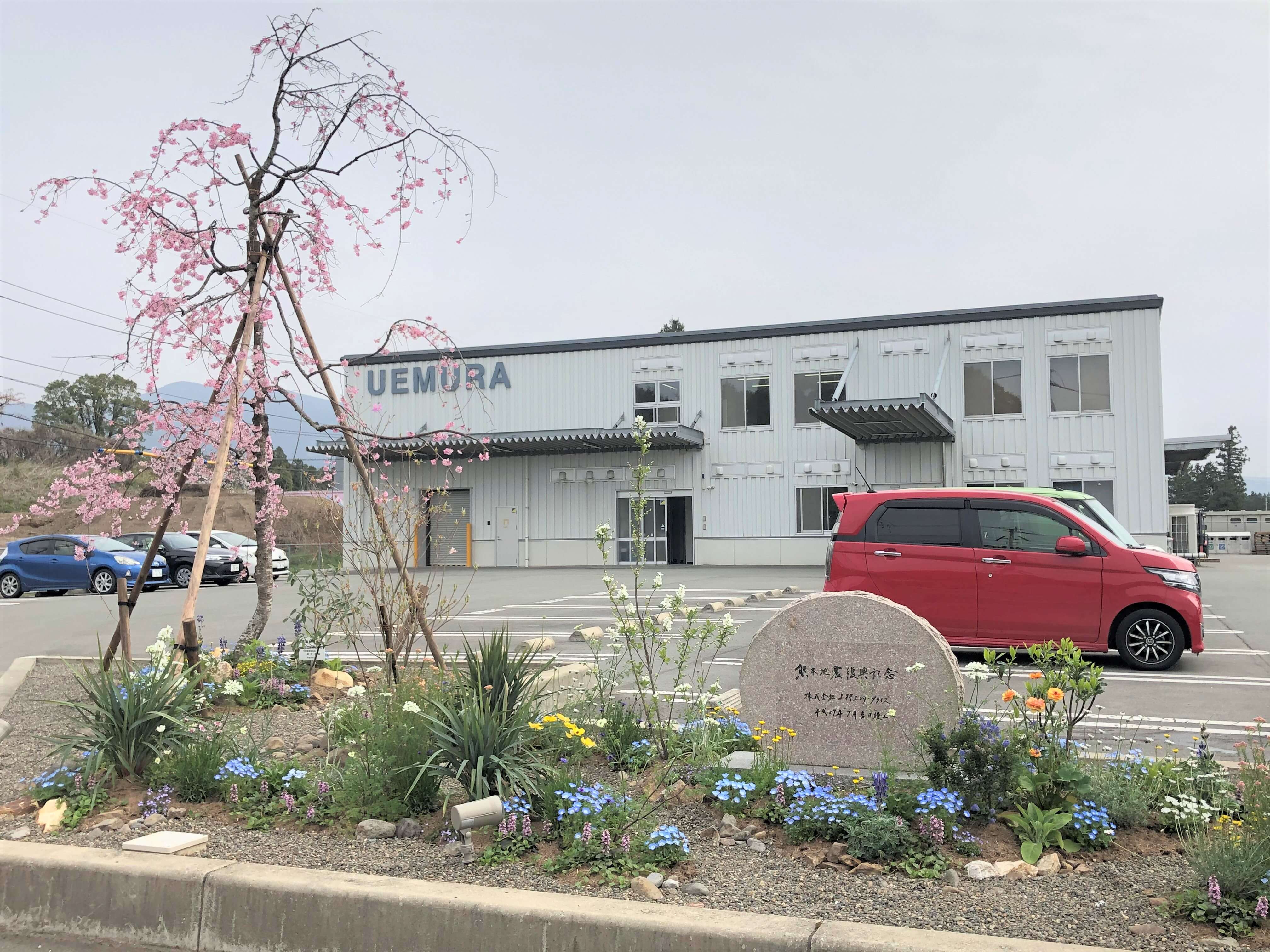
Q1.現場が抱えていた課題について教えてください
製造の進捗が見えないことで右往左往。事前の準備も大変。
当社では、半導体製造装置周りのNC切削加工品のほか、食品業界や化粧品、医療業界まで、さまざまな業界の製品の製造に対応しています。製品の品種は非常に多く、常時500~600種類の製品が工場に流れています。同じ製品の注文が同じ日に2回入ったりすることもあります。 ですが、これまでは進捗を俯瞰して見る手段がなく、どの製品の製造がどの工程まで進んでいるのかを把握するには、現場に出向いて確認するしか方法がありませんでした。基幹システムを操作することで見える情報もあるのですが、複雑な操作をさせるのは作業者にも負荷がかかってしまうので、そのような運用は取れませんでした。
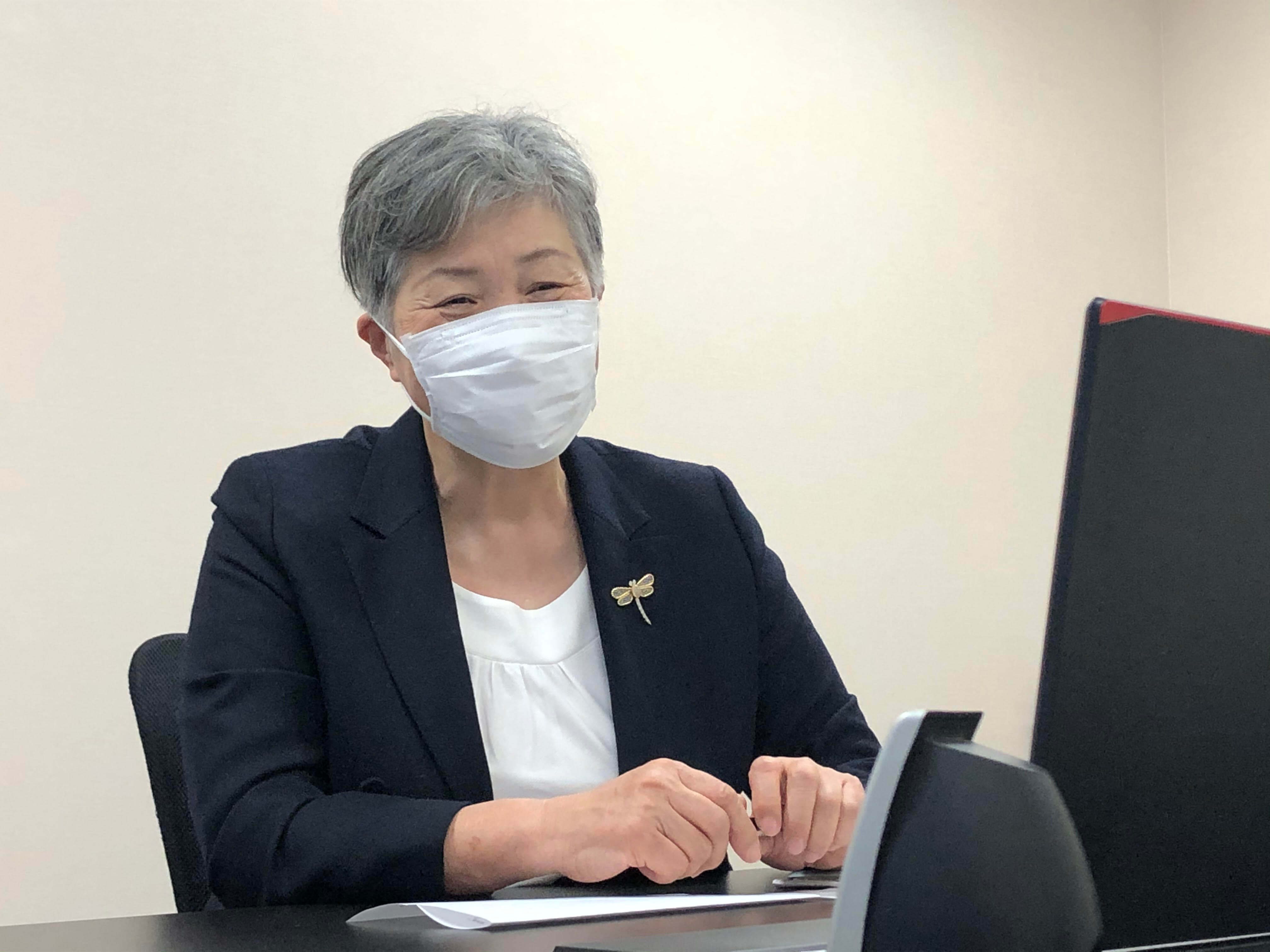
また、工場の人間が製品や作業の内容を一目でわかるよう、あらかじめ図面や現品票といった書類を紙で出力する必要があり、その事務処理の負荷も非常に大きくなっていました。 お客様のニーズにスピーディにお応えするためにも、現場の見える化と情報共有は当社にとって大きな課題となっていました。
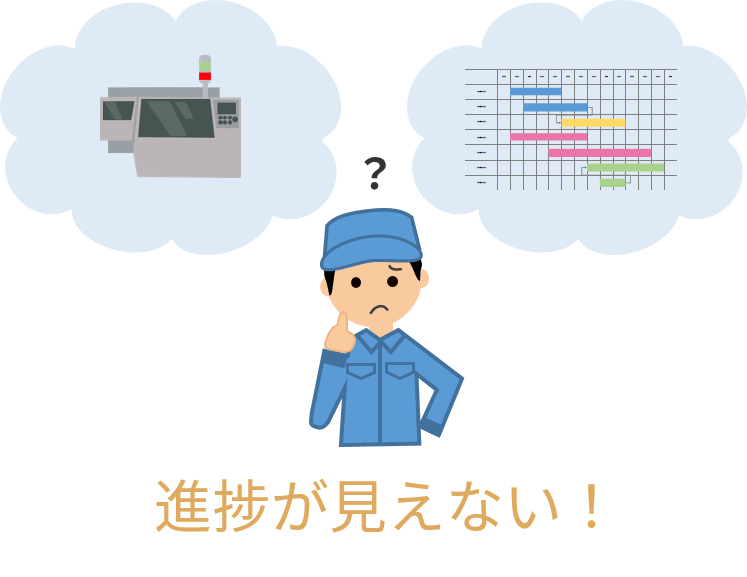
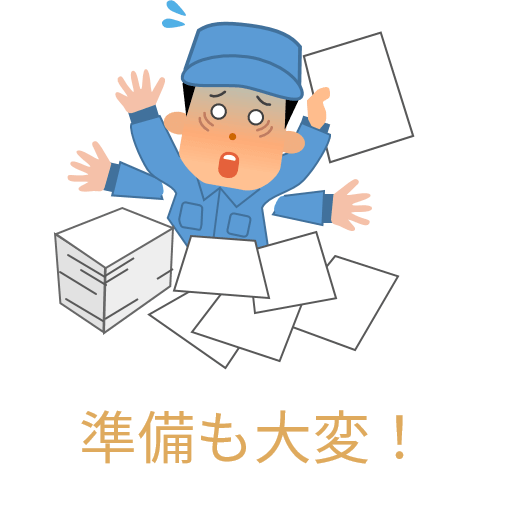
Q2.NAVINECT導入の経緯について教えてください
RFIDにはかなり前から着目。TOPPANの工場見学が決め手に。
RFID(ICタグ)を使った工程管理については、10年以上前からやりたいと思っていました。ただ、そのころはICタグの価格も決して安くはなく、また、システムも「帯に短し襷に長し」のものが多くて、なかなか当社に適したものが見つかりませんでした。 そんななか、TOPPANさんの工場で運用されていた工程管理システムを見せてもらい、これだと思いました。基幹システムとのつなぎ込みのイメージもまさに思い描いていたものでしたので、その後いろいろな打ち合わせも重ねながら当社へのNAVINECT導入を決めました。
≪上村エンタープライズ様における工程の見える化≫
製造指示書の情報と紐づいたICタグを各工程で読み取り 作業開始/終了の実績情報を自動で登録、 リアルタイムにアップロード。 ICタグは自動で読み取られるため ファイルをトレーに入れる/取り出すだけで開始/終了の登録が可能。 基幹システムとの間で、生産の指示情報と実績情報を受送信。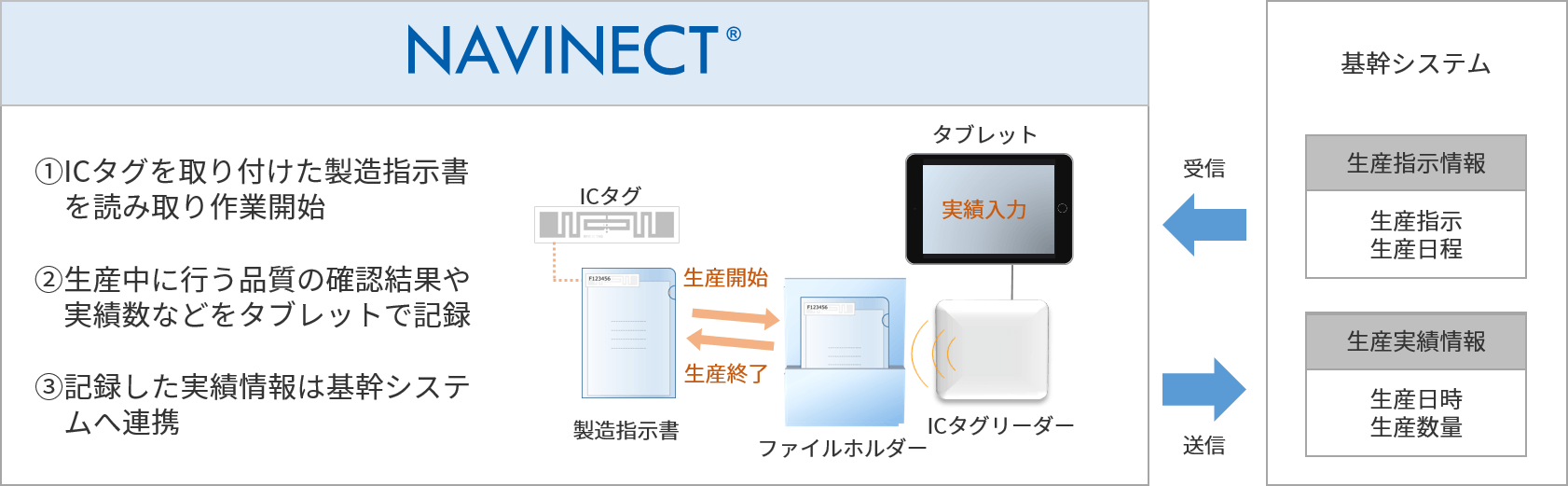
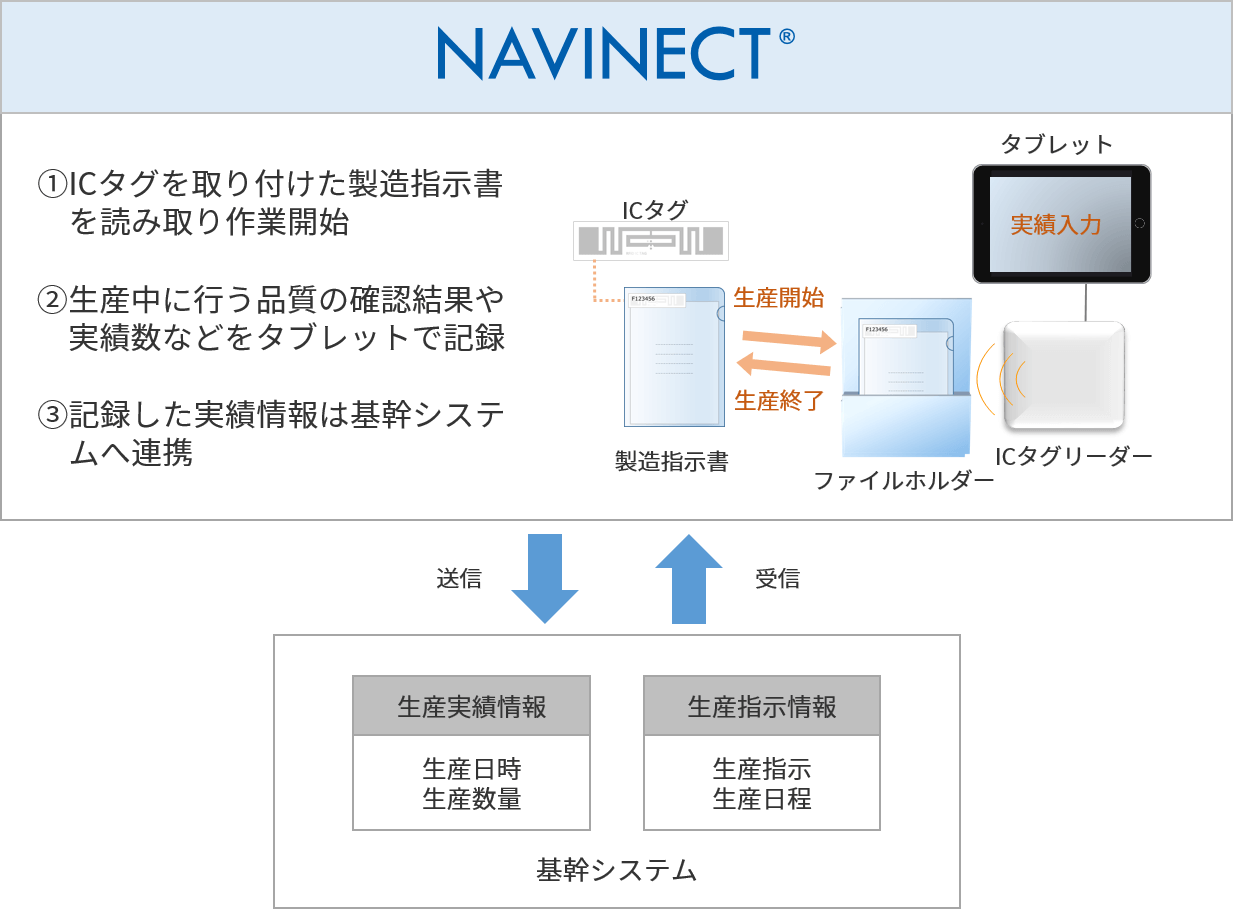

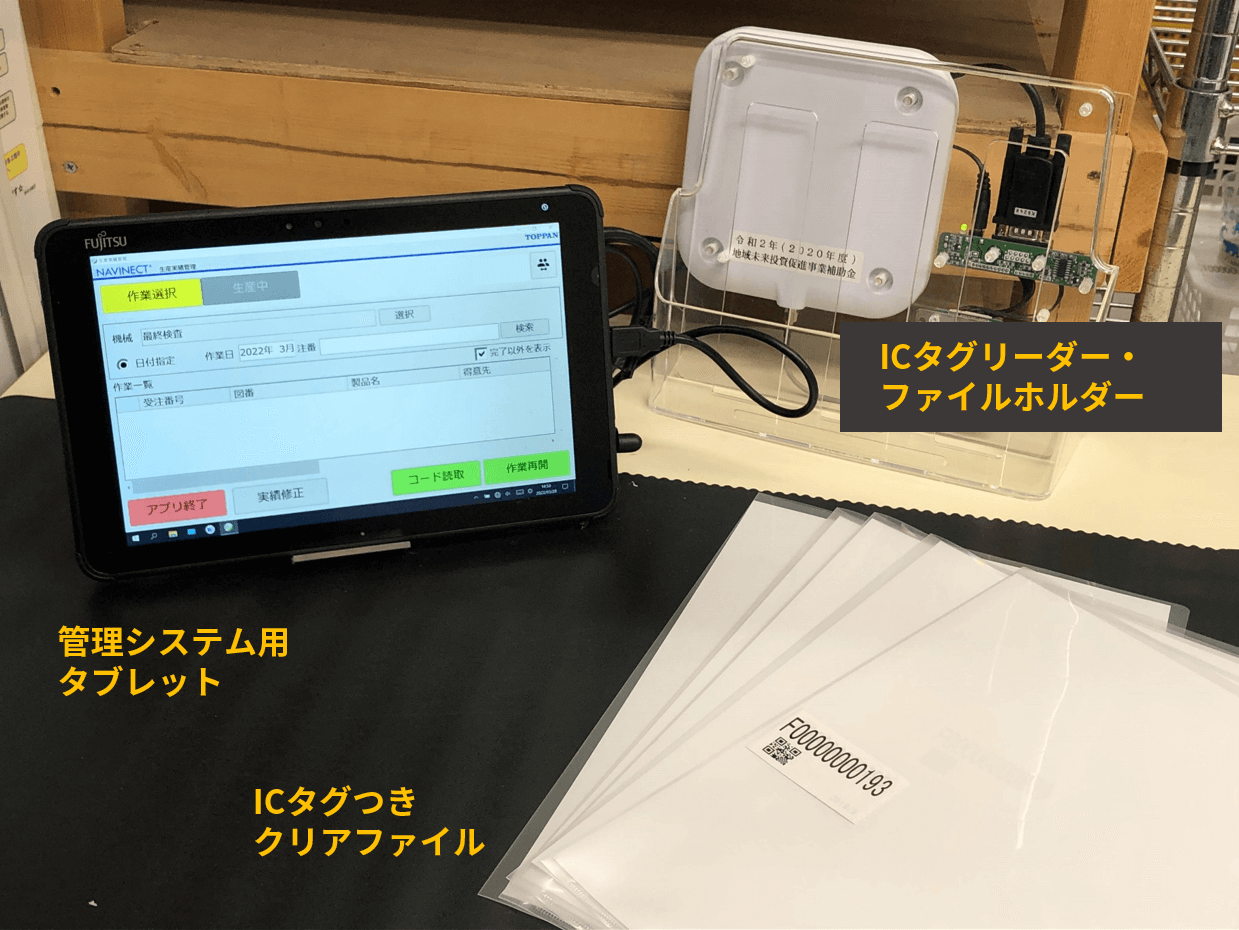
Q3.NAVINECT導入の効果について教えてください
工程の"いま"を把握することで、探す時間をほぼゼロに。ほかにもスケジュールの柔軟性UP、生産性向上など盛りだくさん。
まず何よりも即効性があったのは、製品がどの工程にあるかがリアルタイムにわかるということでした。今までは製品の所在を探すのに現場を走り回っていたましたが、NAVINECT導入後は画面1つでわかります。1日に2~3時間、週に10時間程度は製品を探す時間に取られていましたが、今はそれがほぼゼロになりました。 さらに、工程が見えることで、空いている工程がどこかがすぐ分かります。空いた工程に短納期の別作業を入れることができるなどスケジュールの柔軟性も上がりました。お客さまと電話で会話をしながら管理画面を見て、納期が即答できたりもしています。こういった点はお客さまにもご評価いただけているところです。
現場でいまから行う作業の図面を読ませると、もう一件同じ内容の追加注文が入っていることが判ったりします。その場合は作業をまとめて行うこともできますので、現場の生産性向上にもつながっています。 今まで大変だった事前準備も必要最低限のものを出力すれば済みますし、手書き作業が減ったのでミス・ロスも削減できました。 見える化による効果はこのようにたくさんあるのですが、現場の作業者のアクションとしては”ファイルをトレーに入れるだけ”ですので、作業に影響を与えることもなく、非常に助かっています。
Q4.現場の意識の変化はありましたか?
「管理」から「共有」への意識変化で、皆が前向きに。
NAVINECTの導入にあたり、当初は皆が前向きというわけではありませんでした。今思えばその目的として『「工程の管理」がしたい』という言葉を使っていたためかもしれません。機械も管理され、ヒトも管理され、がんじがらめにされてしまう印象を持ったのでしょう。それがあるときから、『「情報」をみんなで「共有」し活用しよう』、という言葉に置き換わっていきました。そうすると次第に前向きに捉えられるようになり、導入・活用の準備に弾みがついていったように思います。 導入の効果はすぐに見えるかたちで現れましたので、今ではNAVINECTから得られる情報を使った現場の改善に、みんなが前向きに取り組んでいます。長年の苦労が報われた感じがします。これがまさに製造現場のデジタルトランスフォーメーションだと感じています。 NAVINECTを通じて蓄積されるたくさんの情報は会社の財産になると考えています。品質保証の観点、説明責任においても、企業として大きな自信につながっています。
Q5.今後の展望について教えてください
基幹システム連携とデータの更なる活用。モノづくりの会社としての矜持も忘れずに。
ひとつは基幹システムとの連携の部分で、例えば基幹システムが担っていた機能をNAVINECTに置き換えることもできると考えています。 増えていくデータを有効に使う方法も継続して検討しています。データを集計して、判断して、示唆を得る。勉強しながらではありますが着実に進めていきたいです。 ただあくまで私たちはモノづくりの会社です。モノをしっかり作ったうえで、データを取る。データはモノづくりに活かす。優先順位も考えながらブレないようにやっていきたいと考えています。
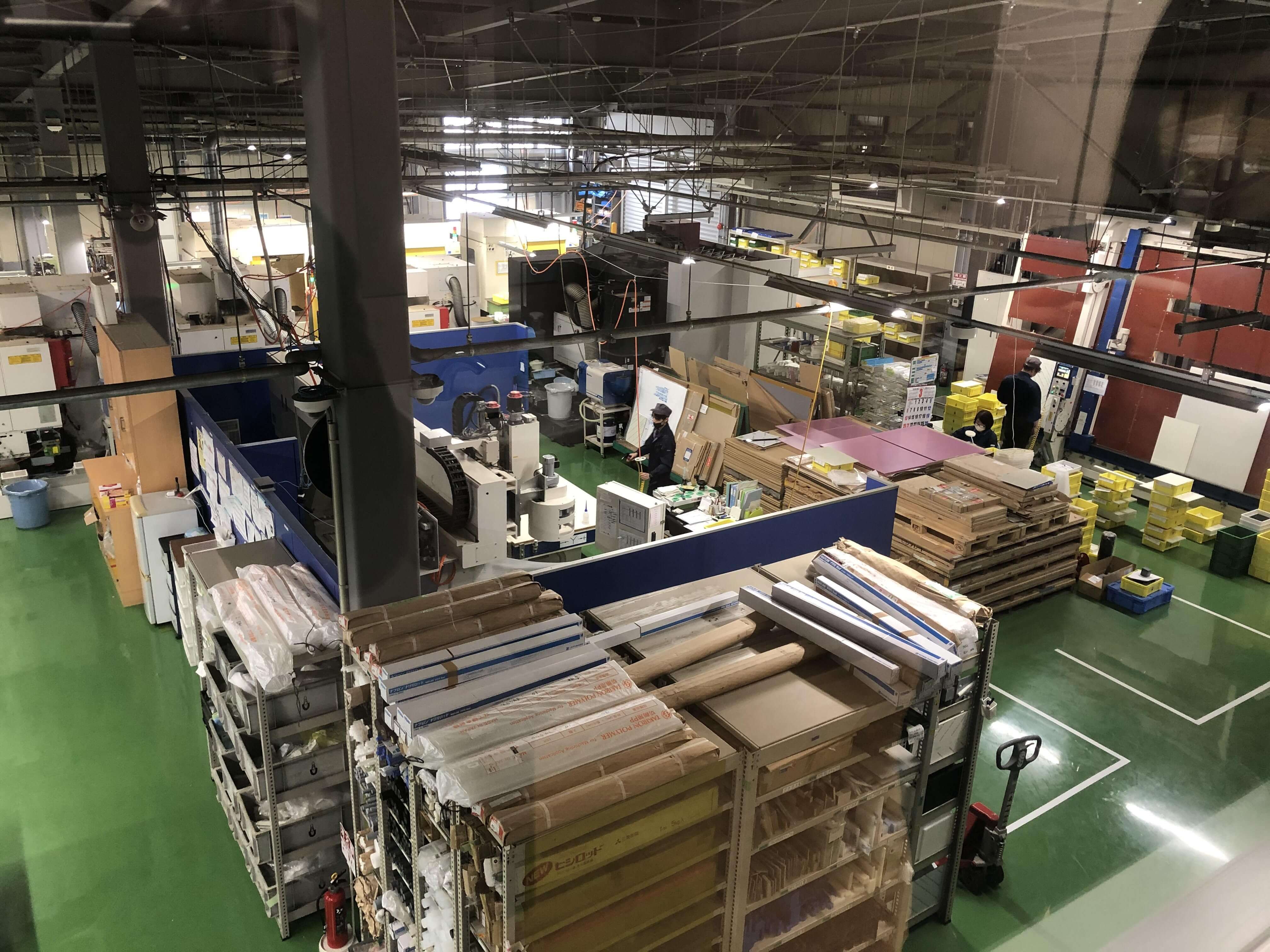
ー 上村社長、貴重なお話ありがとうございました。
課題や導入効果について貴重なお話をいただけただけでなく、最後はモノづくりにかける熱い思いにも触れることができました。TOPPANデジタルではこれからもNAVINECTを通して、モノづくりの現場のDXに悩むお客さまを解決に導いてまいります。
-
「製造管理」パッケージを知る
-
NAVINECTインサイトを知る
-
「RFID」を知る