「充填包装ライン向けDX」とは
TOPPANは、自社工場での改善活動、充填機・包装機の装置販売、包材提供の3つの側面で長年ノウハウを培ってきました。このノウハウに、製造系データインテグレーション技術を掛け合わせソリューションとして提供することで、お客さまの生産現場の生産性・製品の安全性の向上を実現するのが「充填包装ライン向けDX」です。
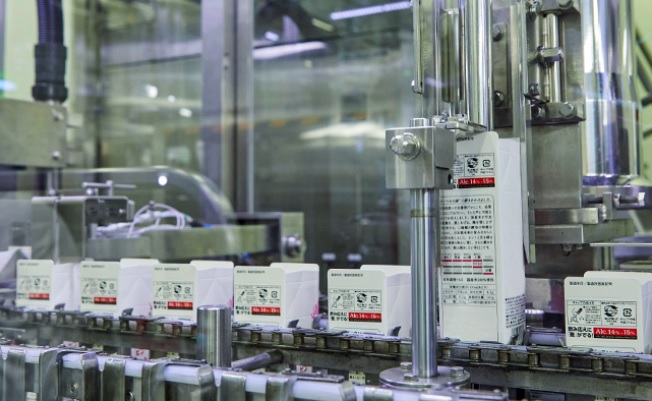
「充填包装ライン向けDX」の特徴
食品・飲料品 製造現場を支援する 製造DX
-
POINT
1 -
充填機・包装機メーカーとの連携によるデータ収集機能標準化 ※ 特許第7120479号
社内の製造知見をもとに、容器成形不良や液漏れ不良防止のため、異常兆候を監視するためのセンシング機能と、装置メーカーと連携したデータ収集機能を充填機・包装機へ標準機能として搭載し提供します。これによりコストを削減するとともに、装置導入後の即時運用が可能です。また、「見える化」・「警報化」・「誤投入防止」を行う製造支援アプリケーションを活用することで、現場の生産性改善を支援します。
-
POINT
2 -
包材個々の製造履歴把握による品質保証
生産時の「条件・材料・検査結果・装置情報」のデータを、包材に印字された個体識別用コードに紐づけ管理します。アプリケーションによる検索により、不良発生時の「影響範囲の特定」「原因究明」が短時間でおこなえます。品質保証を強化でき、製品の安全性・顧客への信頼性の向上します。
また、工程異常の原因調査に活用することにより良品率改善につなげることが可能です。将来的にはTOPPANの供給する包材の製造履歴と紐付けることにより、より一層の品質保証体制の構築を目指しております。
-
POINT
3 -
充填・包装工程に合わせパッケージしたシステムの提供
TOPPANは、パッケージ系・コミュニケーション系・エレクトロニクス系の事業で多くの商材の製造拠点にて、社内で開発した製造DXシステムを用いて生産性向上の活動を実施してきました。また、パッケージ系では自社開発した充填機・包装機の運用、販売や包材を提供してきた実績があります。この長年培った運用ノウハウによるアプリケーション群により装置データの監視・分析・制御を行うことが可能です。
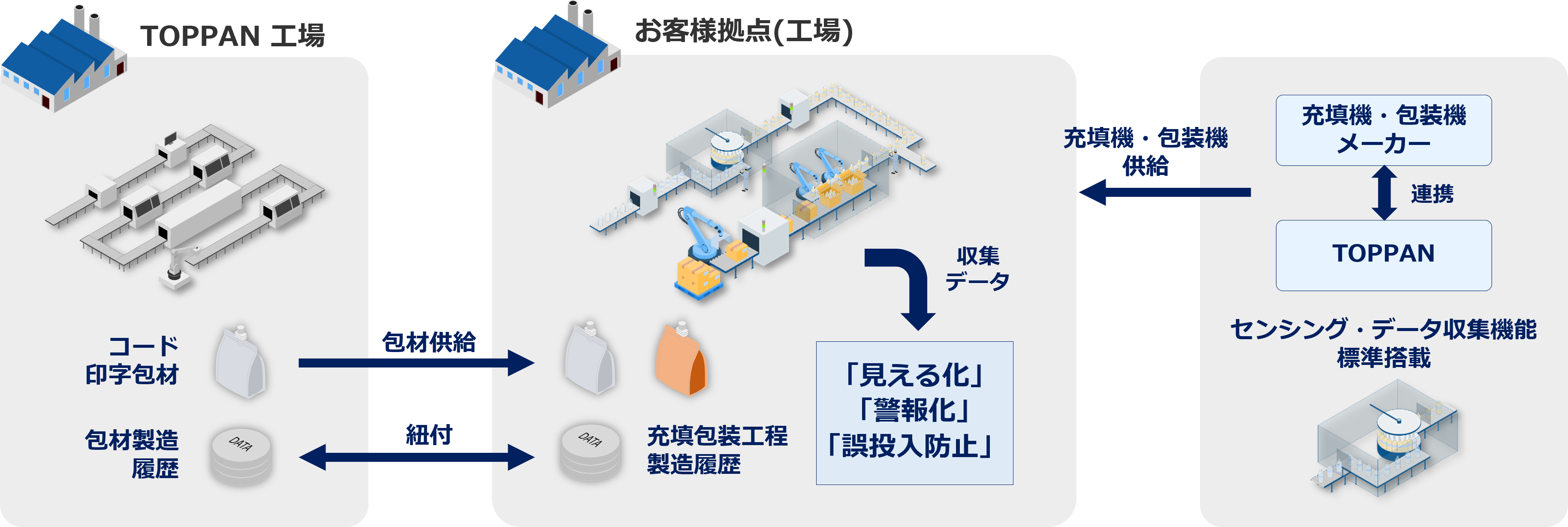
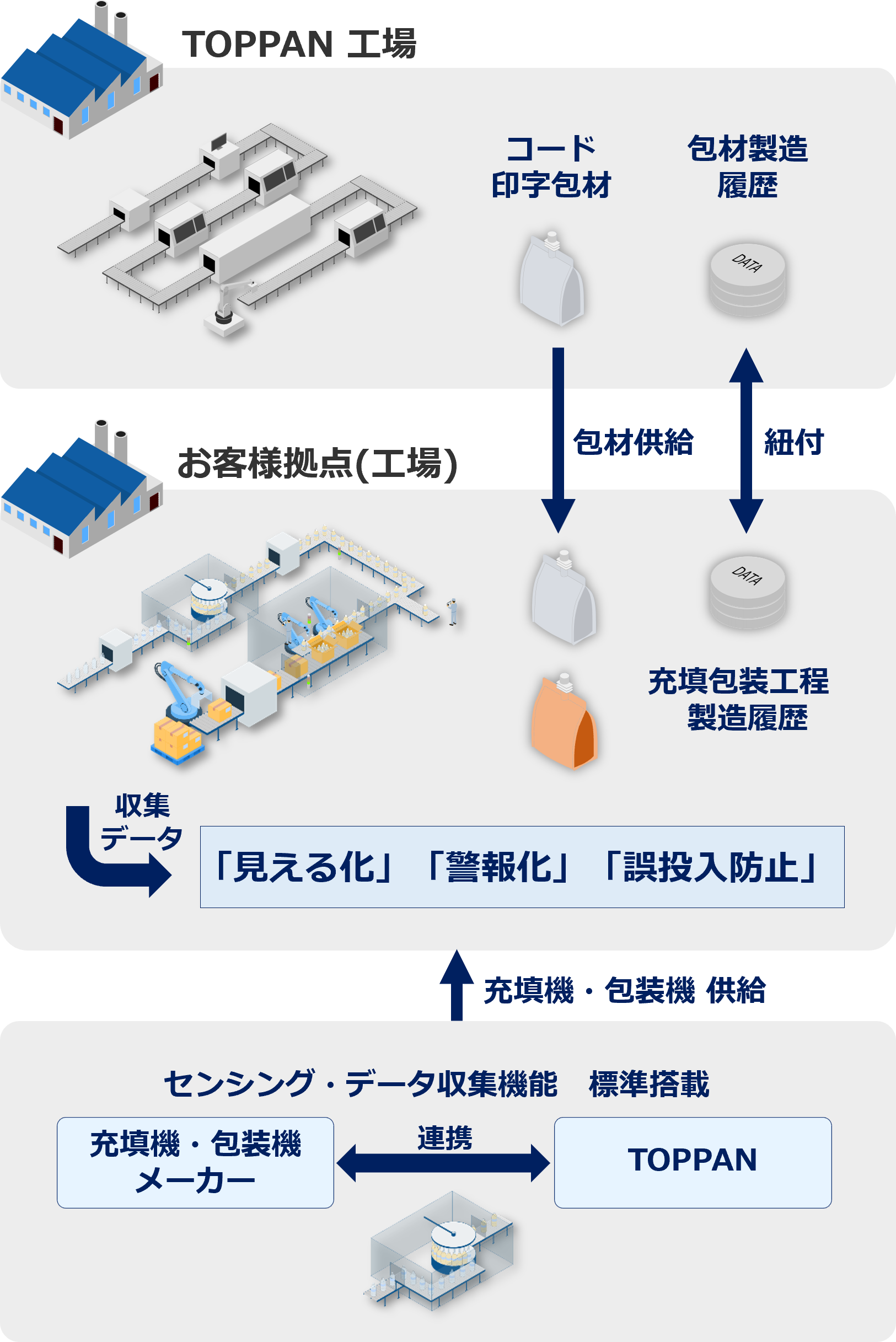
「充填包装ライン向けDX」
5つのアプリケーション
「充填包装ライン向けDX」では、包材に印字されたコード、充填機・包装機に標準搭載されたデータ収集機能で収集したデータを5つのアプリケーションにより、「機械の変化」・「プロセス条件の変化」・「製造履歴」を「見える化」・「警報化」することで、生産停止や不良発生を防止することが可能です。
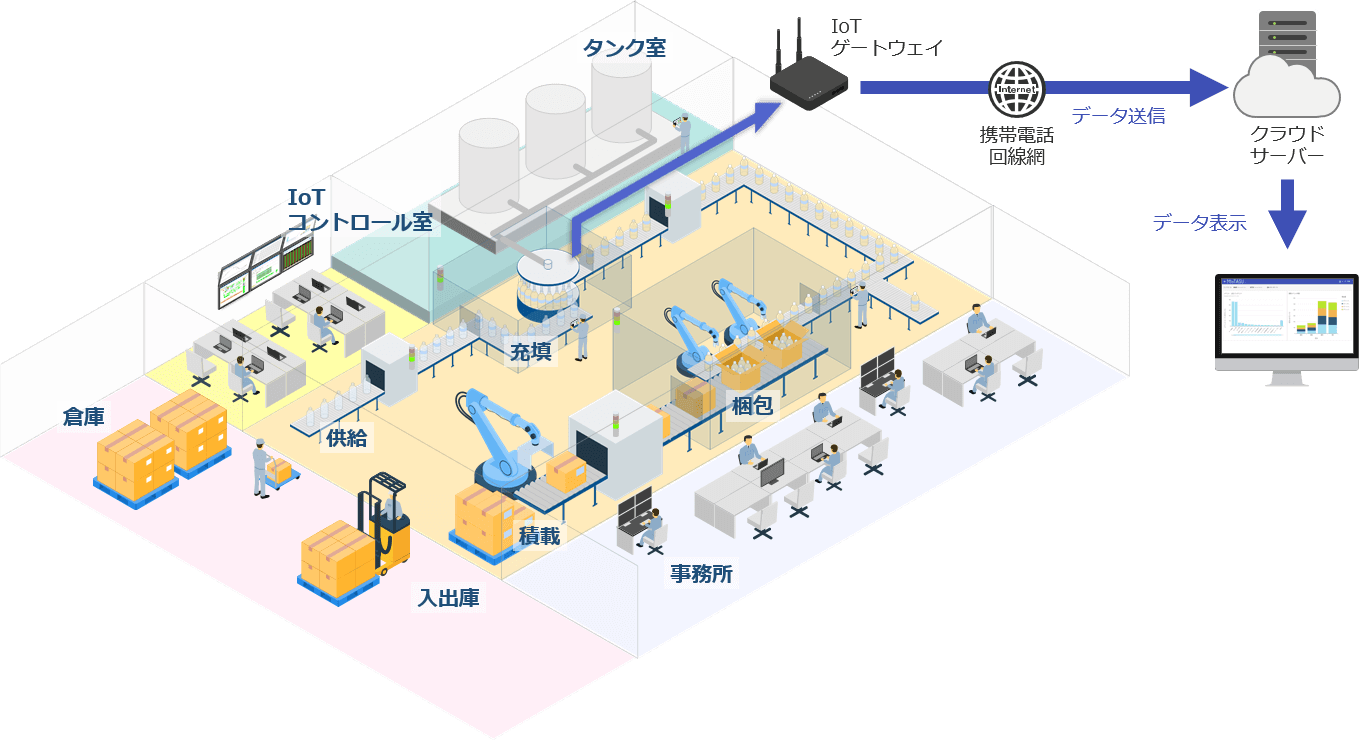
保全レポート
-
稼働状態監視
-
異常兆候監視
-
誤投入防止制御
-
製造履歴参照
(トレーサビリティ)
監視・制御などの現場監視に利用 ※製造現場で稼働
-
-
稼働状態監視
装置の運転状態をリアルタイムで監視します。異常発生時には対象装置・アラーム内容を製造現場・事務所のモニター上に通知します。
詳細を見る>>
-
-
異常兆候監視
品質・保全に関わる各種データを収集、時系列での変化を監視します。警報範囲を設定することにより異常の予兆を通知します。
詳細を見る>>
-
-
誤投入防止制御
投入資材、金型治具を使用前に照合することで、選定間違いや設置ミスを防止します。異常時は生産を開始しません。
詳細を見る>>
-
-
製造履歴参照
(トレーサビリティ)
包材に印字された製品個々の識別番号と収集データ(検査結果・プロセス情報・稼働情報・材料情報)を紐付、生産履歴を検索可能です。
中・長期的なデータの管理/分析に利用 ※クラウド上で稼働
-
-
保全レポート
長期傾向の把握
異常項目の自動集計
充填機の付帯機能です。装置に標準搭載されたIoT機能を活用した装置データの中・長期的な変化の見える化/集計機能を提供し、装置の保全活動を支援します。
詳細を見る>>
「充填包装ライン向けDX」活用事例
POINT 1
活用事例①:成形温度の常時監視による包材成形の安定化POINT 1
活用内容
充填包装工程において、包材成形の安定化には、溶着のための加熱・冷却条件管理が重要です。
装置にセンシング機能を標準で搭載し、データの推移を常時監視することで、異常の兆候をとらえ不良発生を防止することが
可能です。
活用事例
センシング機能追加
成形時の温度分布を測るサーモグラフィーカメラを追加
※センシング機能は本サービスの標準機能には含まれておりません。
動作検証、装置への標準搭載を随時進めております。
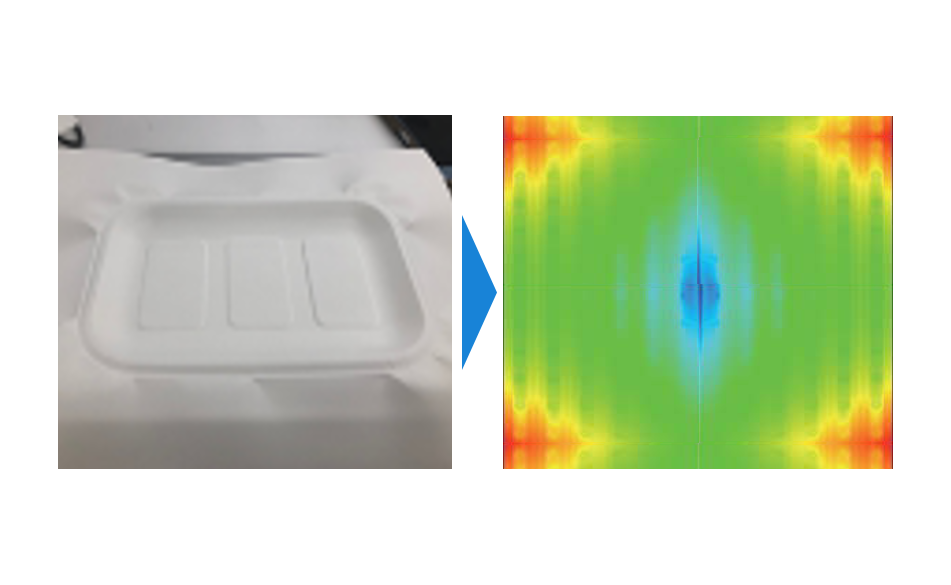
異常予兆監視
数値化した温度データを常時監視し、異常値検出時は、アラームで担当者に通知
※溶着温度・冷却温度・溶着圧力・ヒーター(製品)位置など
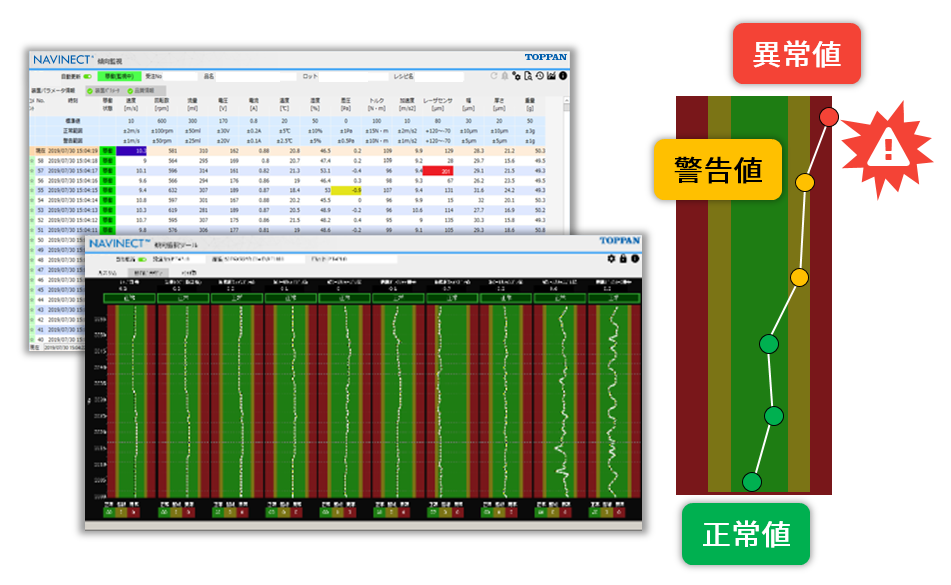
期待される導入効果
不良発生前に異常検知・処置が可能となり、不良の防止・良品率が向上。
段取り調整時間の削減。
POINT 2
活用事例②:包材の識別コードを利用した異常発生時の早期対策POINT 2
活用内容
包材に印字された個体識別コードを元に、製造過程のデータを分析することで、原因の特定が容易になります。
また、影響範囲の特定も効率的に行え、製品の安全性向上に寄与します。
下記は、品質不良情報から、異常起因箇所(ヒーター異常)を発見した例です。
活用事例
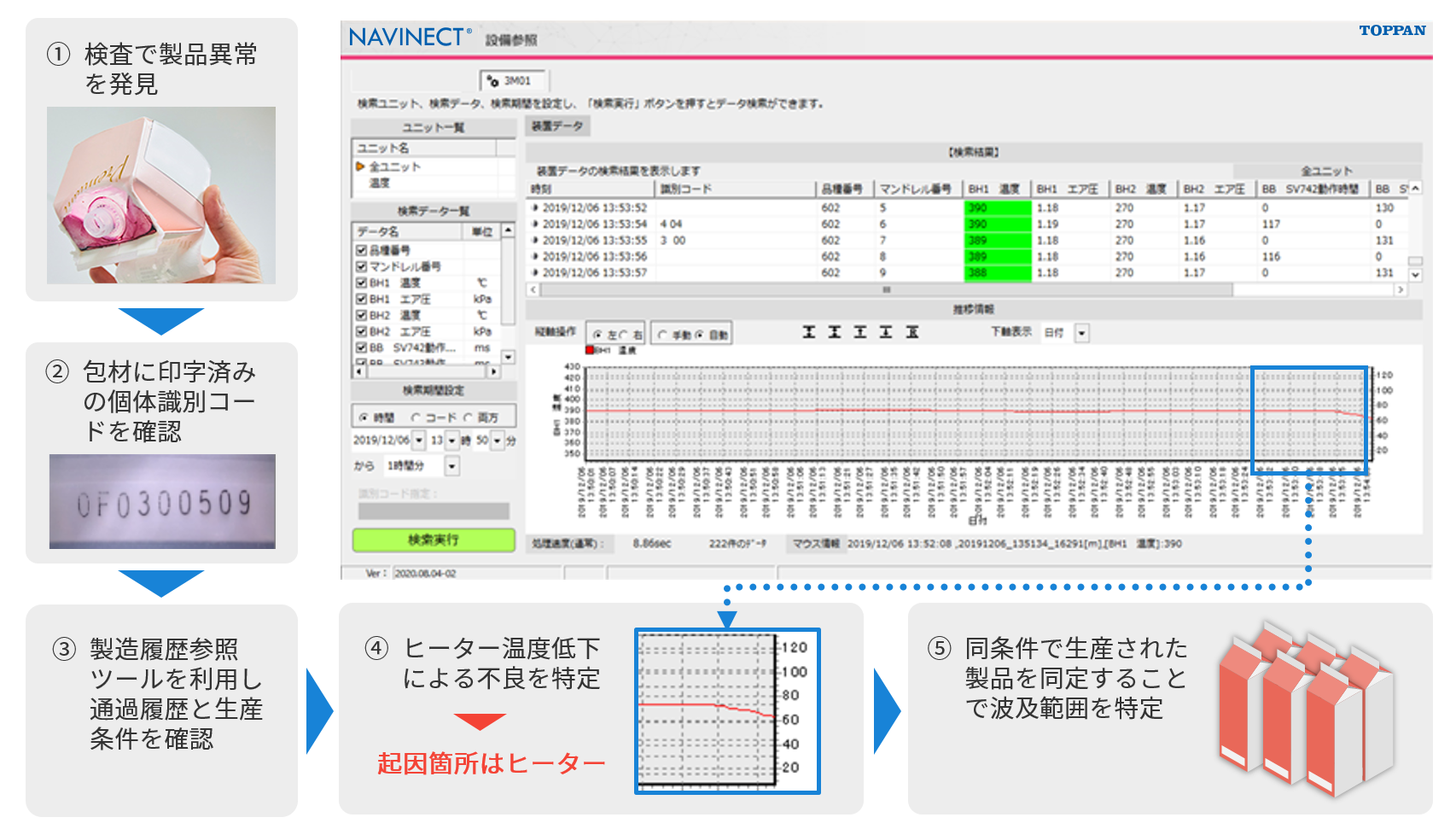
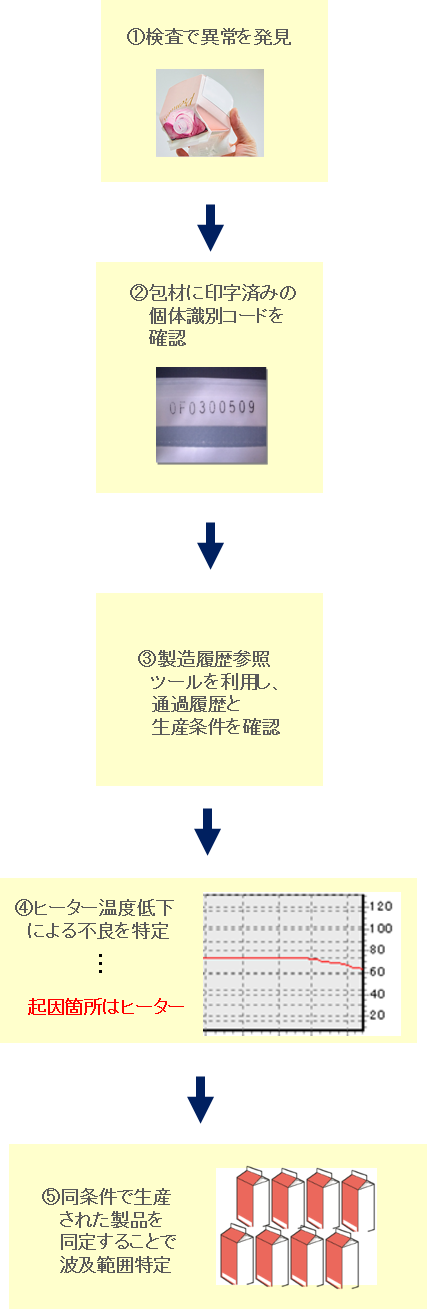
期待される導入効果
不良発生時の原因特定が容易となり、調査時間の短縮が可能。また、影響範囲の特定も効率的に行え、
製品の安全性(品質保証)が向上
POINT 3
活用事例③:金型取付ミスの事前検知による不良発生防止POINT 3
活用内容
成形品質上の重要な管理項目である金型のセット位置状態をセンシング。従来までの微調整を繰り返した条件設定方式でなく、
良品範囲を数値化し、作業標準化と調整ミス(人的ミス)防止に寄与します。
活用事例
-
金型ヒーターのセット位置を監視、位置ずれを検知し警報で通知。異常が是正されるまで生産は開始せず、不良品生産を防止する。
-
使用する資材・部品を事前に装置設置・デジタル帳票と照合、誤投入を防止可能。
期待される導入効果
位置ずれでの生産を停止することで、不良品の生産を防止。セット位置の見える化による品質の安定。