更新日:2023.01.26
「製造業におけるデータインテグリティとは【各論編①】」では、データライフサイクルの起点としての、デジタルデータの記録についてご紹介しました。 本コラムでは、デジタルで記録されたデータを製品品質の維持・向上へ活用するための手法としての「SPC(統計的工程管理)」と「個体トレーサビリティ」について記載します。 どちらも食品や製造などの分野において古くから耳にする言葉であり、伝統的な品質管理手法として知られています。 しかし、これらの手法を製造の現場に落とし込み、実践できている企業は多くはなく、それ故に品質・性能偽装やデータ改ざん、リコール隠しのニュースを耳にする機会が後を絶たない現状があります。 デジタルデータの記録をベースとしたこれらの品質管理手法は敷居が高いもののように聞こえてしまう一方で、品質の維持・向上以外にも副次的メリットを含むものであることまではあまり知られていません。 まずは、SPC(統計的工程管理)についてご紹介します。
製造業を支えるSPC(統計的工程管理)とは
SPCとは「Statistical Process Control」の略語であり、日本語で「統計的工程管理」と訳されます。 工程における異常の兆候検知と改善、品質の維持・向上を目的とするSPCは、工程に関する平常時の数値情報(=規格)と、センサーなどで自動的且つ継続的に計測される稼働状況の傾向に関する数値情報を比較することで、データ上の乖離(=異常の兆候)の有無を管理する手法です。 具体的には、製品の品質に影響を及ぼす以下のようなデータを、各種センサーを用いて数値的に管理します。 ■ 寸法、硬度、温度などの製品に関するもの ■ 出力、振動などの生産設備に関するもの ■ 気温、湿度など製造現場の環境に関するもの 「不良品の発生」を検知するのではなく、不良品の発生に繋がる可能性のある「工程異常の兆候」を検知し処置・分析することで、不良品や工程における異常発生を未然に防ぎ品質を底上げする点がSPCの特徴です。 SPCは、自動車産業の国際的な品質マネジメントシステムであるISO/TS16949で要求されるツールの1つでもあり、製造現場におけるベーシックな品質管理手法となりつつあります。
【SPC導入効果イメージ】
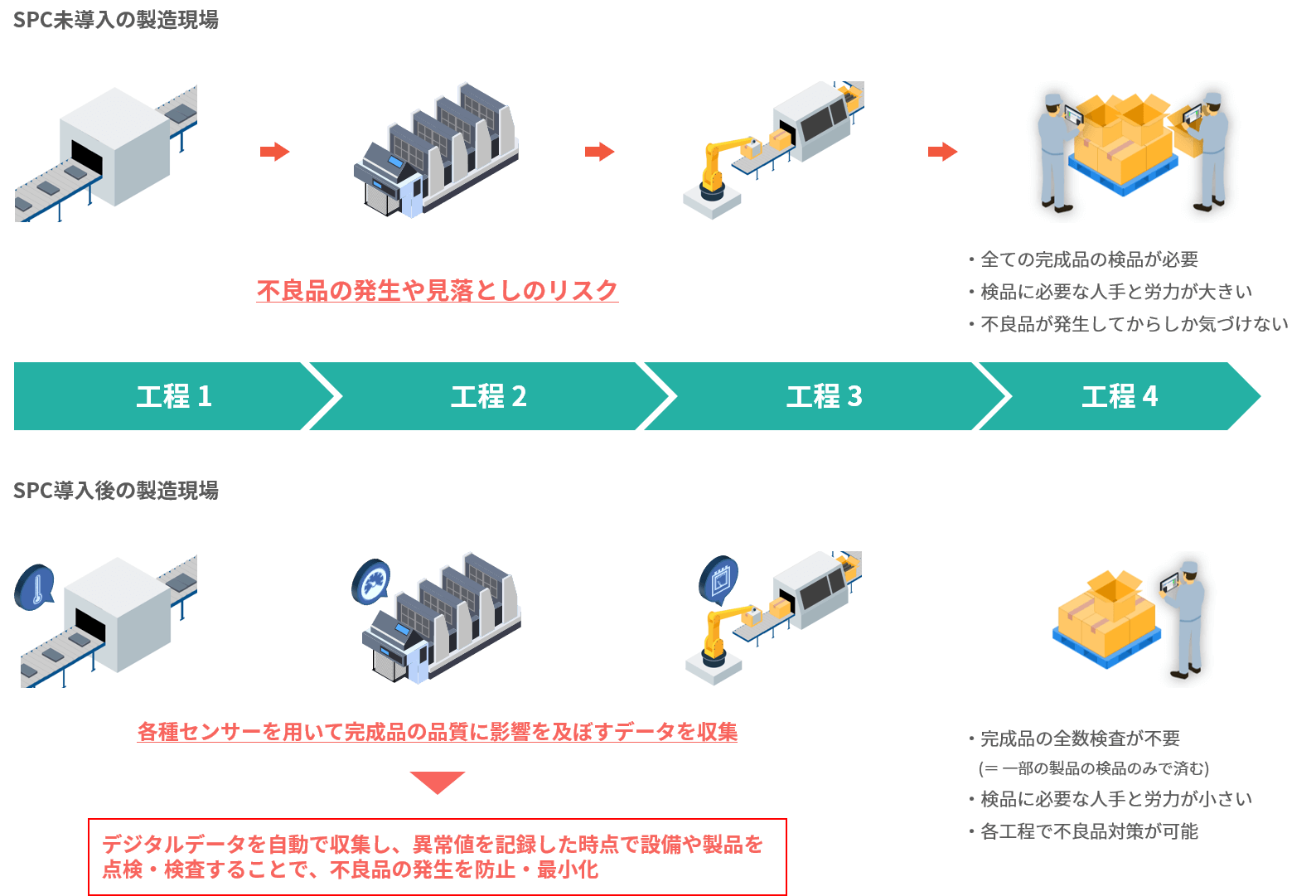
SPC(統計的工程管理)によるデータ収集の一例
各種センサーによって収集されるデータは「管理図」というグラフを用いて数値化・可視化し、管理することが一般的です。 管理図を読み取る際には、統計学的に偶発する正常な範囲の数値的なばらつきと、工程上で発生した異常やその兆候に起因する数値的なばらつきの違いに注目します。
管理図の構成
管理図は以下に示す軸から構成されます。
【管理図イメージ】
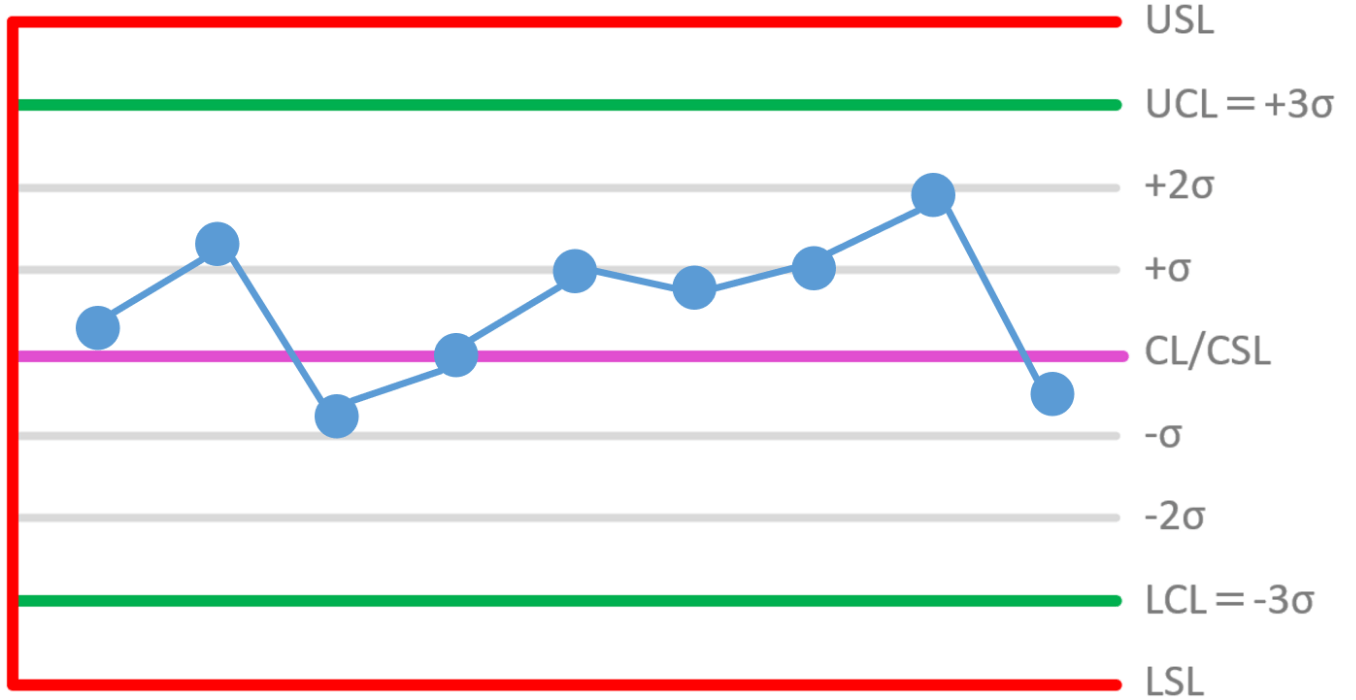
-
CL / CSL(中心線)
過去の計測の実績から算出した正常時の数値をグラフの中央に置きます。
-
1σ ~ 4σ
σ(標準偏差)は平均値からの”ばらつき”の大きさを示す記号です。
数字が大きくなるほど平均値から離れた位置にいることが分かります。統計学上、数値の分布が±3σの範囲に収まる確率が99.73%とされます。 -
UCL(上方管理限界値)
前述のσが+3σの状態の値を指します。この値を上回る数値を異常の兆候として調査の対象とする指標になります。
-
LCL(下方管理限界値)
前述のσが-3σの状態の値を指します。この値を下回る数値を異常の兆候として調査の対象とする指標になります。
-
USL(上方規格限界値)
前述のσが+4σの状態の値を指します。グラフの上限として設定されます。
-
LSL(下方規格限界値)
前述のσが-4σの状態の値を指します。グラフの下限として設定されます。
±3σ以内の範囲にほとんど全ての計測数値が収まることを利用し、その範囲を逸脱した値を異常の兆候と判断することが多くあります。 「±3σ」という統計学に基づいた客観的な判断基準が取り入れられている点と、収集データの遷移が継続的に視認性良く確認できる点が管理図の構成の特徴です。
管理図が示す製造現場の異常兆候
工程における異常の兆候を管理図で判断する際には、±3σからの逸脱だけが判断基準となるわけではありません。 ±3σ以内に収まる範囲であっても、以下のようなグラフの特徴が見られた場合には計測箇所において異常の兆候が発生していると判断する場合が多いです。
① N回連続で上側(下側)の値である
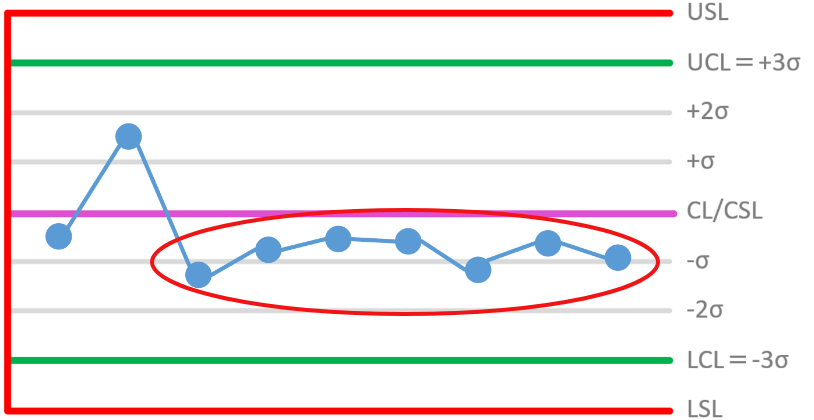
正常な値たる中心線を上回り続ける(下回り続ける)場合は、計測箇所の点検が必要な可能性があります。一般的に、6~9回連続で片側の数値が続く場合には注意が必要です。
② N回連続でXσを越えている
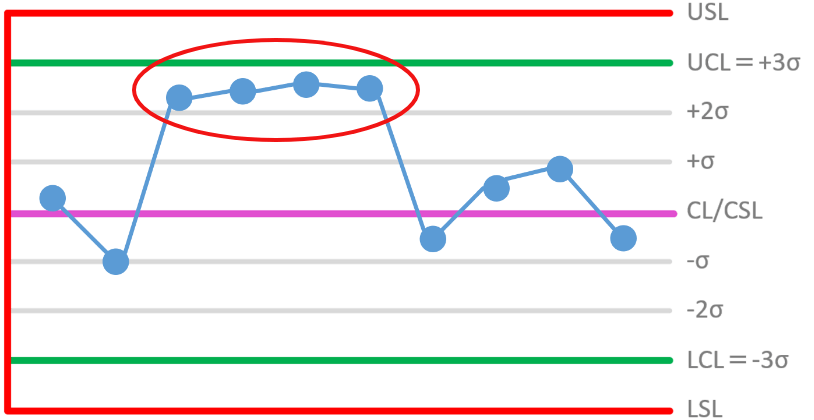
中⼼線から離れている状態が続く場合は異常の兆候の可能性があります。
③ N回以上の計測で上昇 / 下降している
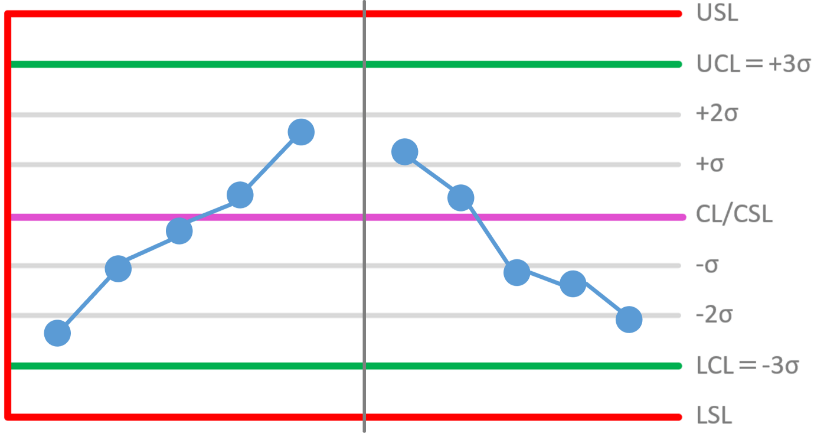
各限界値に関わらず、任意の回数以上連続で計測値が上昇あるいは下降している状態です。
④ N回連続で交互に打点されている
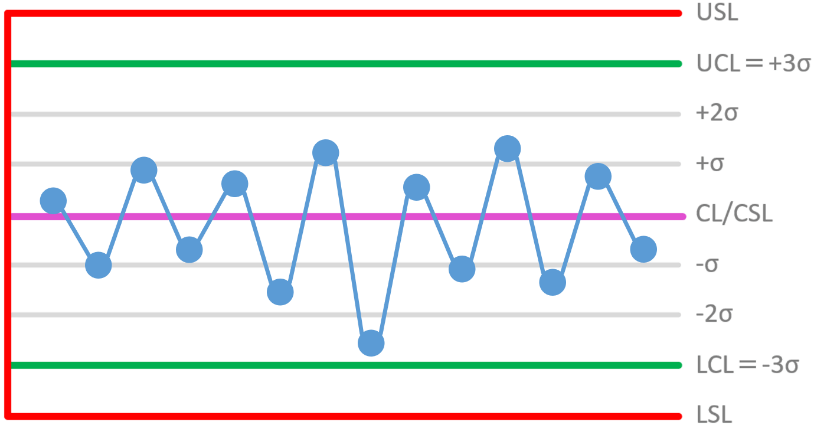
故意にデータが作成 / 改ざんされている可能性があり、注意が必要です。
グラフ上のこれらの傾向以外にも、管理図から異常の兆候を読み取る際の判断基準は多数存在します。 SPCを実践する上では、管理図がどのような値を示したら工程に危険が迫っていると判断するか、事前に判断パターンを洗い出しておくことが必要となります。 一方で、これらのパターンを全て把握し、収集されるデータを常時、マンパワーで監視し続けることは困難です。 いつでも容易に遡ることが出来るデジタルデータの蓄積と、異常の兆候発生を自動で作業者や管理者が認知できるような仕組みの導入が重要となります。
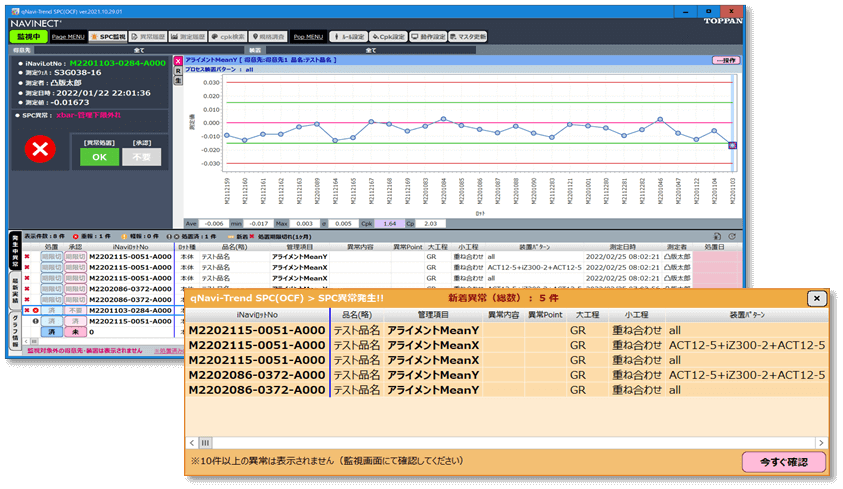
管理図に異常の兆候が見つかったら
実際に異常の兆候が見られた際に、どのようなフローで対処や記録を行うのか、予め決めておくことがSPCの効果を高める上で重要となります。 また、処置と同時に再発防止に向けた原因の究明も必要不可欠となりますが、原因の分析ツールとして製造の現場で多く用いられる「QC七つ道具」と呼ばれる7つの分析手法をご紹介します。
① グラフ
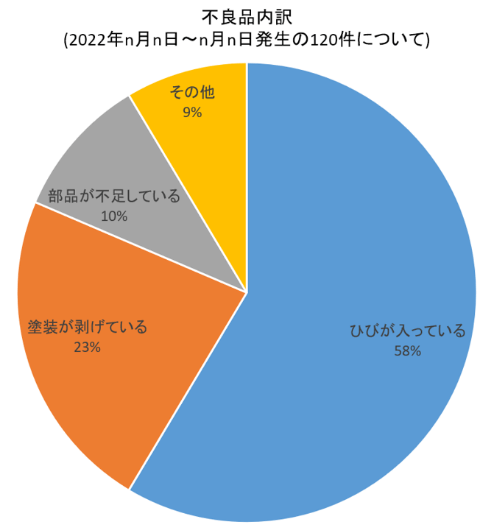
さまざまな形状のグラフで、数値の大小や推移を可視化します。
② 散布図
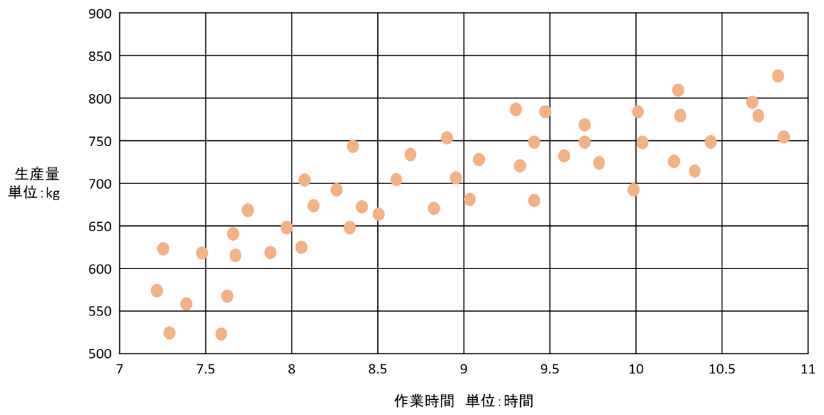
2つの異なる要因の相関性の有無を見抜くためにデータをプロットし使用します。
③ 層別

データを様々な階層で切り分け、特徴を見抜きます。 例:時間別、作業者別など
④ チェックシート
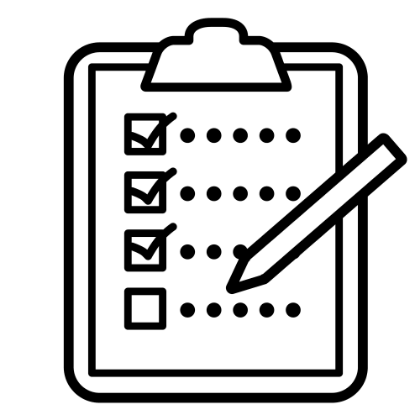
予め決められた、作業に関する確認項目などを記録したシートで、人為的ミスや漏れが無いかを確認します。
⑤ 特性要因図
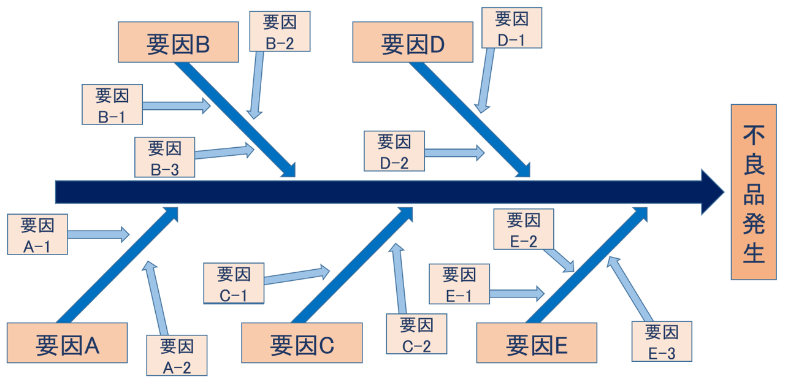
不良品発生を「特性」として、その発生要因を洗い出し、各要因の発生要因を更に細分化し洗い出します。
⑥ パレート図
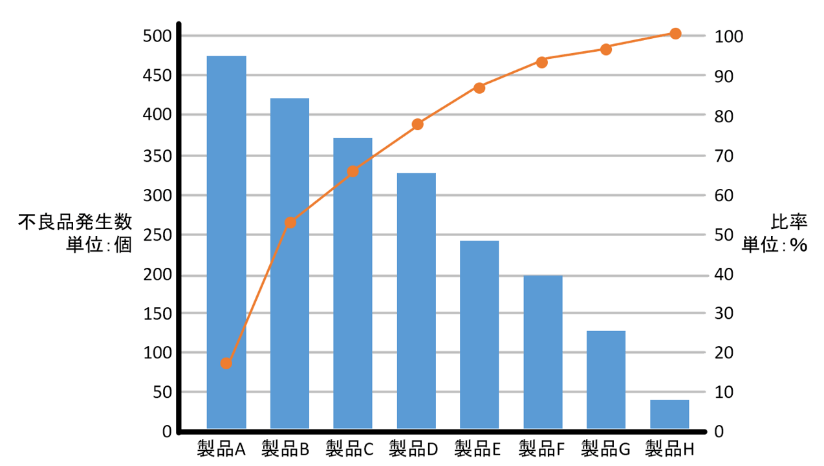
横軸の各項目の数を累計数で割り、件数と割合を表した図です。全体の中で各項目が占める割合を可視化します。
⑦ ヒストグラム
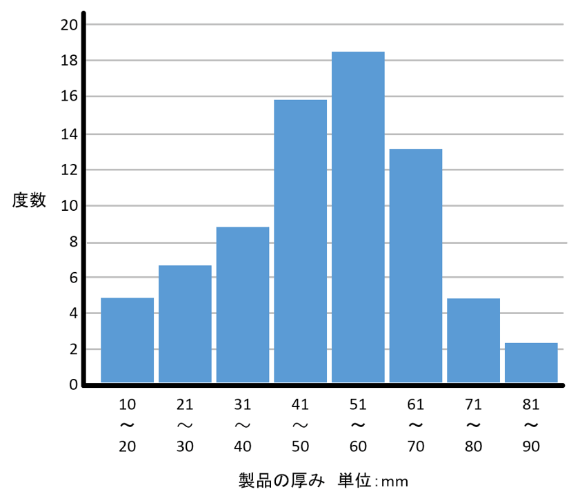
連続的な値を持つデータを幾つかの区間で分けて並べることで、それぞれのばらつきや平均を見極めます。
異常の兆候を発見した際には、デジタルで収集・蓄積された客観的なデータをQC七つ道具のような手法で分析することで、的確な原因究明と工程の改善に向けたアクションの策定が可能となります。 また、管理図や製造設備の分析に加え、どのような異変がどの工程で出やすいかなど、これらを集計データとして分析し工程の改善に役立てる活動も重要です。以下の画面のように各種データがデジタルで収集されている場合、アラートの一覧化や分析など、発見以降のアクションを効率的且つ正確なものとすることが可能です。
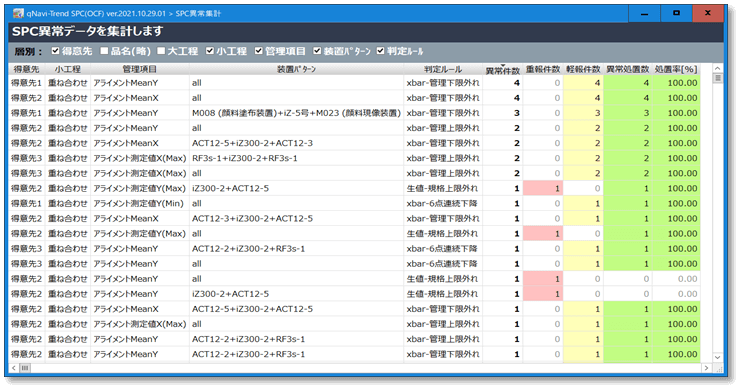
SPC(統計的工程管理)導入のメリット
これまで、SPCは工程における品質の維持・向上を目的とするものとしてご紹介しました。 製造品質の維持・向上は不良品の発生頻度の抑制に繋がります。品質を高水準に維持できていない製造現場においては、不良品の発生頻度が高くなり、より強固な検品体制の構築が必要になります。また、万が一不良品が世に出回った際には、一例として以下のような対応が必要となります。 ■ 世間への不良品発生の周知・注意喚起 ■ 問い合わせ・クレーム対応窓口の開設 ■ 不良品の回収、廃棄作業 ■ 製造工程の停止、原因究明 ■ 得意先への謝罪対応、再製造 etc... SPCによる品質の維持・向上は、不良品の発生に紐づくこのような無駄な業務や費用のリスクを低減し、安定した製造現場の実現に繋がります。 また、上記の不良品に関するリスクヘッジ以外にも、企業は以下のようなメリットを享受することが可能です。
-
タイムリーな工程の最適化
完成品の検品だけでは知り得なかった、生産設備や製造環境の情報を継続的に収集することが可能となることで、各種設備のリニューアルや製造ラインの再検討を含む工程の改善の手立てを、異常の兆候の発生と同時に打つことが出来るようになります。
-
工程における品質管理の人員の最適化
生産設備や製造環境に関するデータが継続的に収集できることにより、より少ない人員でより高頻度な工程の品質管理を実現し、コストパフォーマンスを向上させます。
-
完成品の検品へ割り当てる人員の最適化
製造工程の異常の兆候を早期に検知できることに加え、それらに起因する不良品の発生も抑止可能となり、人海戦術で行っていた完成品の検品に要する人員を最適化することが可能です。
製造現場におけるSPC(統計的工程管理)の実現
これまでご紹介したような、管理図を用いたモニタリングやQC7つ道具を活用した原因の究明は、製造現場の品質を維持・向上させ運用改善にも繋がり得る手段です。しかし、収集する各種データを紙ベースで記録していたり、データの管理図への落とし込みを作業員自身が行っていては、先に挙げた人員の最適化などの効果は得られず費用ばかりがかかってしまいます。 「製造業におけるデータインテグリティとは【各論編①】」で述べた通り、誤った記録や改ざんを防止する観点からも、これらのデータ収集はデジタルにより自動で記録され続け、人の手を極力介さないことが理想的です。 SPCをデジタルで実現できるような製造業向けの管理システムは既に世に出回っていますが、製造現場への導入負荷を極力低減し、ご紹介したようなSPCのメリットを最大化させるためには、以下のような条件を押さえたものが有効と考えます。 ■ 各種データを自動且つ継続的に記録可能 ■ どの拠点にいる従業員でもリアルタイムに情報へアプローチ可能 ■ データの記録から異常の検知、原因究明までをワンストップで実施可能 このような仕組みを導入することにより、客観的なデータに基づく生産品質の向上とコストメリットに裏付けられた生産・業務効率の向上の両立が可能となります。
終わりに
SPCを活用した管理手法について実例を含めて紹介して参りましたが、製造品質の維持・向上に繋がる手段はSPCに限りません。 SPCと類似する「SQC(統計的品質管理)」や、次回のコラムで紹介する「個体トレーサビリティ」も、SPCと異なる品質維持・管理の手段として挙げられます。 それぞれの手段の特徴と製造現場の抱える課題やありたい姿を照らし合わせ、最も効果のある手法を見極め、導入していくことが重要です。
関連記事
-
NAVINECTの特徴を知る
-
NAVINECT製品を知る