更新日:2023.01.26
「製造業におけるデータインテグリティとは【各論編②】」では、品質管理の手法としてのSPCをご紹介しました。製造工程における設備の稼働状況などを数値化・統計化し、正常時と異常の兆候が見られる時の差分を可視化し検知するこの手法は、生産設備や工程の環境を主な対象とし、品質を管理するものです。 個体トレーサビリティ(以下、トレーサビリティ)は、工程ではなく原材料、部品、製品ひとつひとつやロットごとに着目し、いつどのような工程を経て製造され、どこに出荷されていくかという一連の流れを管理する手法です。 製品に関わるデータの完全性や正確性を客観的に担保し、データインテグリティを実現するものとして既に幅広い製造業で実践されつつあるこのトレーサビリティについて、本コラムではご紹介します。
製造業におけるデータインテグリティとは【総論編】 はこちらから>
製造業におけるデータインテグリティとは【各論編①】 はこちらから>
製造業におけるデータインテグリティとは【各論編②】はこちらから>
トレーサビリティとは
「トレーサビリティ」は、追跡を意味する「Trace」と可能性や能力を意味する「Ability」という言葉が組み合わされた造語です。 トレーサビリティの実現は、昨今トレンドになっているSDGsで定められている「つくる責任つかう責任」の目標にも深く関わっており、「どこで誰によってどのようにつくられたのか」や「どこに流通していったのか」を把握する企業の社会的責任を果たすことに繋がります。 トレーサビリティには、原材料の段階から製品として製造 / 流通 / 販売 / 消費されるまでのサプライチェーン全体を記録し追跡する広義の意味と、ある1つの企業や工場など特定の範囲内においてどのような原材料や部品を集め、どのような工程を踏まえて製品が製造されたかを製品単位で記録し追跡する狭義の意味があります。 製造業におけるトレーサビリティは後者の狭義の意味合いで語られることが多く、本コラムでも後者のトレーサビリティを指すものとします。
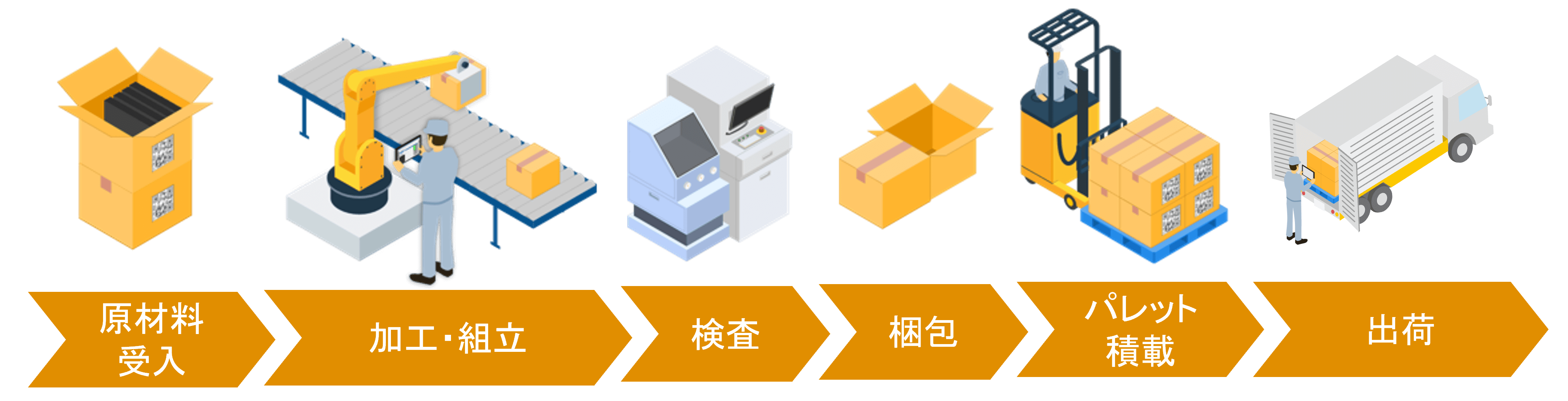
製造業にトレーサビリティが求められる背景
トレーサビリティが世に浸透した背景には、製造現場における不良品発生や製品情報の改ざんなどの不正に対するリスク対策の強化があります。 2000年代前半に発生したBSE(狂牛病)の問題を受け、牛の個体情報の管理が義務付けられたことでトレーサビリティというキーワードは一時的なトレンドとなりました。 製造現場における導入の必要性を企業に対し意識付けたきっかけは、同じく2000年代からニュースに取りざたされることが多くなった、食品業界における賞味期限の偽装や自動車業界における大規模なリコール問題など、消費者に影響を及ぼしかねない品質問題の頻発でした。 これらの問題発生を受け、製造に関わる幅広い業界で、不良品が発生した際に原因となった工程箇所やタイミングを客観的なデータとして追跡できるような仕組みであるトレーサビリティを導入する動きが加速しました。 「製造業におけるデータインテグリティとは【各論編②】」でご紹介した自動車産業の国際的な品質マネジメントシステムであるISO/TS16949では、SPCと同様にトレーサビリティの仕組みの構築を自動車メーカーに対して求めています。 しかし、例えば自動車メーカー1社がトレーサビリティを導入するだけでは、原材料の入荷元や製品の出荷先の工程における品質を追跡することは出来ません。サプライチェーン全体で広義のトレーサビリティを成立させるには、サプライチェーンを構成する全製造 / 流通の現場で狭義のトレーサビリティが導入される必要があります。 エンドユーザーに安全な製品を届けるという社会的責任を、製造に関わる全てのステークホルダーで果たす必要が生じたことが、トレーサビリティ普及の背景となりました。
個体ID付与を通じたトレーサビリティの実践
トレーサビリティは、原材料や製造物に個体IDを付与するところから始まります。この個体IDが、製造履歴の遡及を可能とします。 個体IDを付与する具体的な手段としては以下のようなものがあります。 ■ シリアルナンバー ■ 1次元バーコード ■ 2次元コード(QRコード) ■ RFID etc... 各種リーダーを用いて工程上の要所でこれらのコードを読み取ることで、製品が各工程を流れるタイミングなど予め定められた必要情報を自動で収集可能となります。 どの個体IDの付与手段も現役で使用されているメジャーな手段ですが、近年は「RFID」が使用される機会が増えています。 RFIDは、個体IDの付与と情報の読み取りという点では1次元バーコードやQRコードと同じですが、他のコードより離れた位置からの読み取りが可能である点や、読み取りだけでなく新たな情報の書き込みもできるという点で、より詳細な製品情報を追跡可能となることが特徴です。
個体ID付与と収集データの紐づけの流れ
実際の製造現場では、工程の特性に応じた複数の個体ID付与手段が組み合わされて運用されています。
以下に示すのは、工程に沿った個体IDの付与と、IDに紐づけられるデータ収集の流れの一例です。
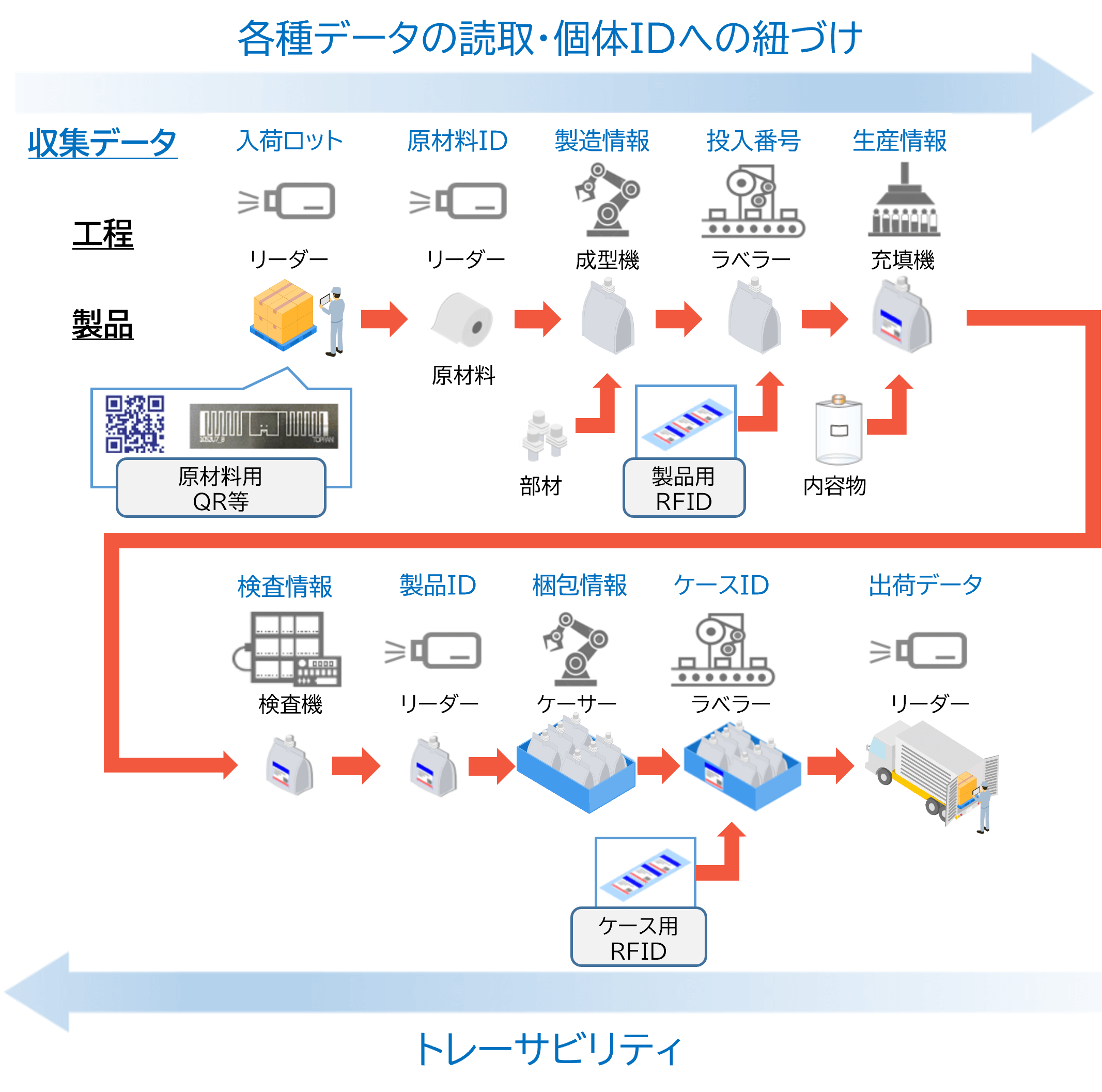
工程ごとに付与された個体IDや紐づけデータは、管理アプリケーションで可視化されます。一つの完成品に関する情報をツリー構造で一覧表示し、製品が通過した最初の工程から最後の工程までの各製造履歴(作業者・装置・材料・製造手法)を可視化します。
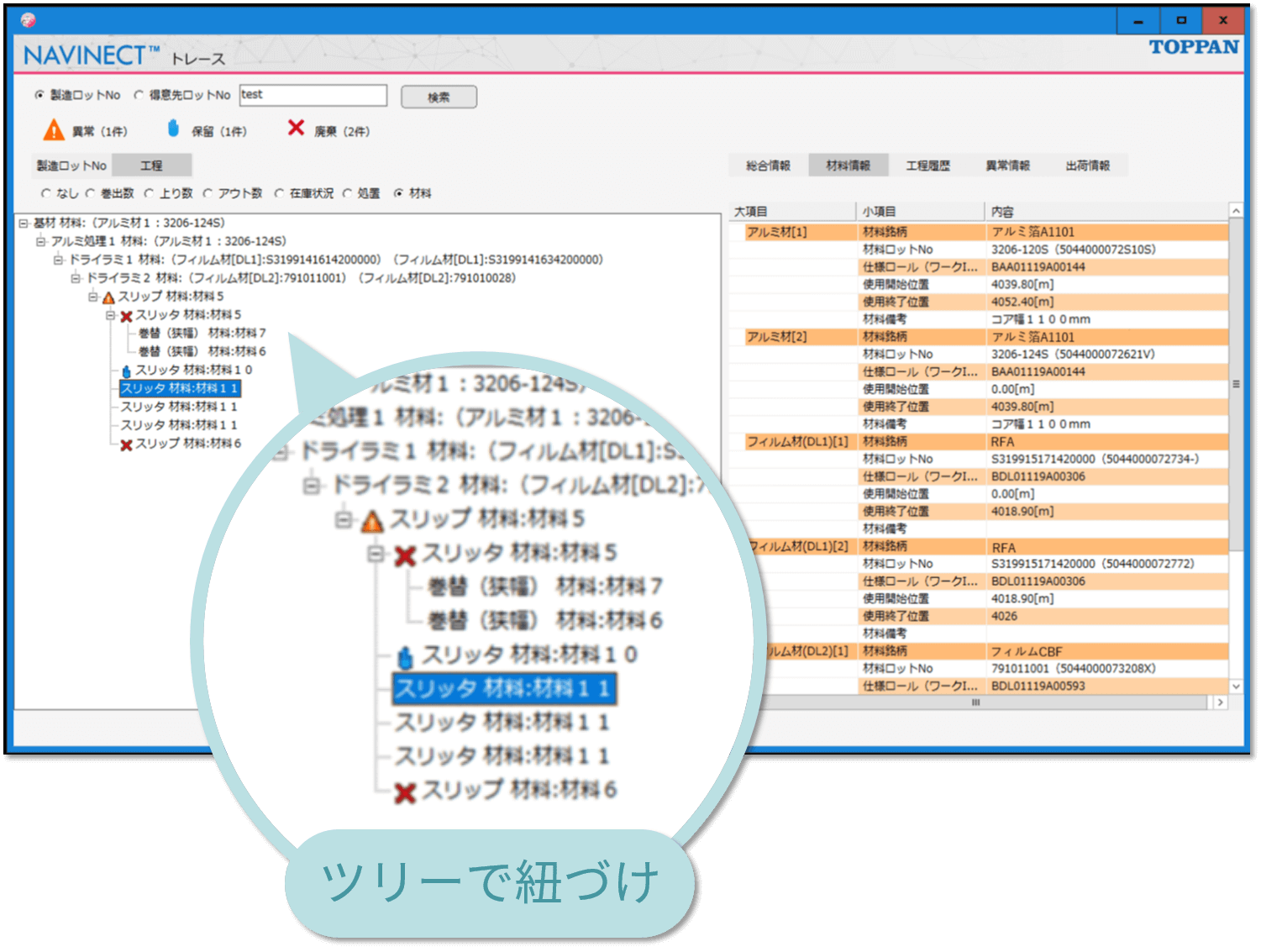
製品に異常が見つかったら
不良品など製品の異常が発見された際には、製品に貼り付けられたコードやシリアルナンバーを基に、製造されたタイミングにおいて生産設備や工程の環境に異常が無かったかを確認します。この確認が、継続的に計測されているデータが紙ベースではなくデジタルで管理されていることで、正確且つスムーズな対応が可能となります。 その工程で不良品発生の原因が明らかになった際には、異常が発生していた期間に製造された個体のIDの範囲を照合します。
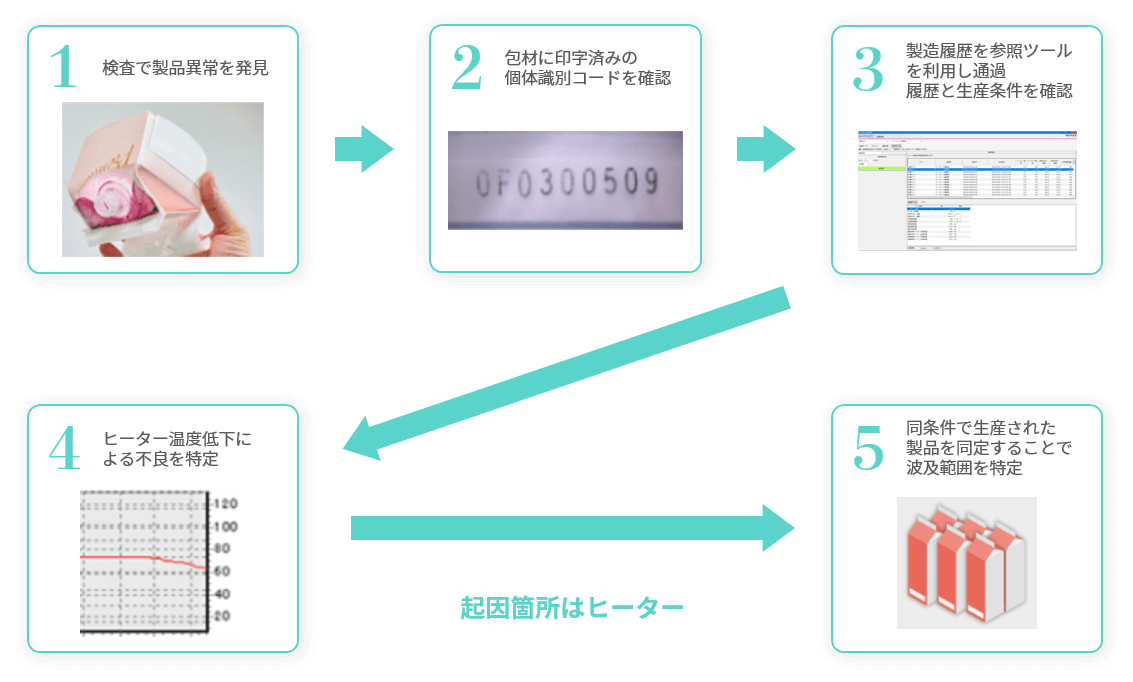
不良品の個体IDからそこに紐づくデータを検索・一覧化できることに加え、工程や生産装置・日時からその条件下で製造された製品のIDを参照できる管理システムを導入することにより、スムーズな不良品の発生範囲特定が可能となります。
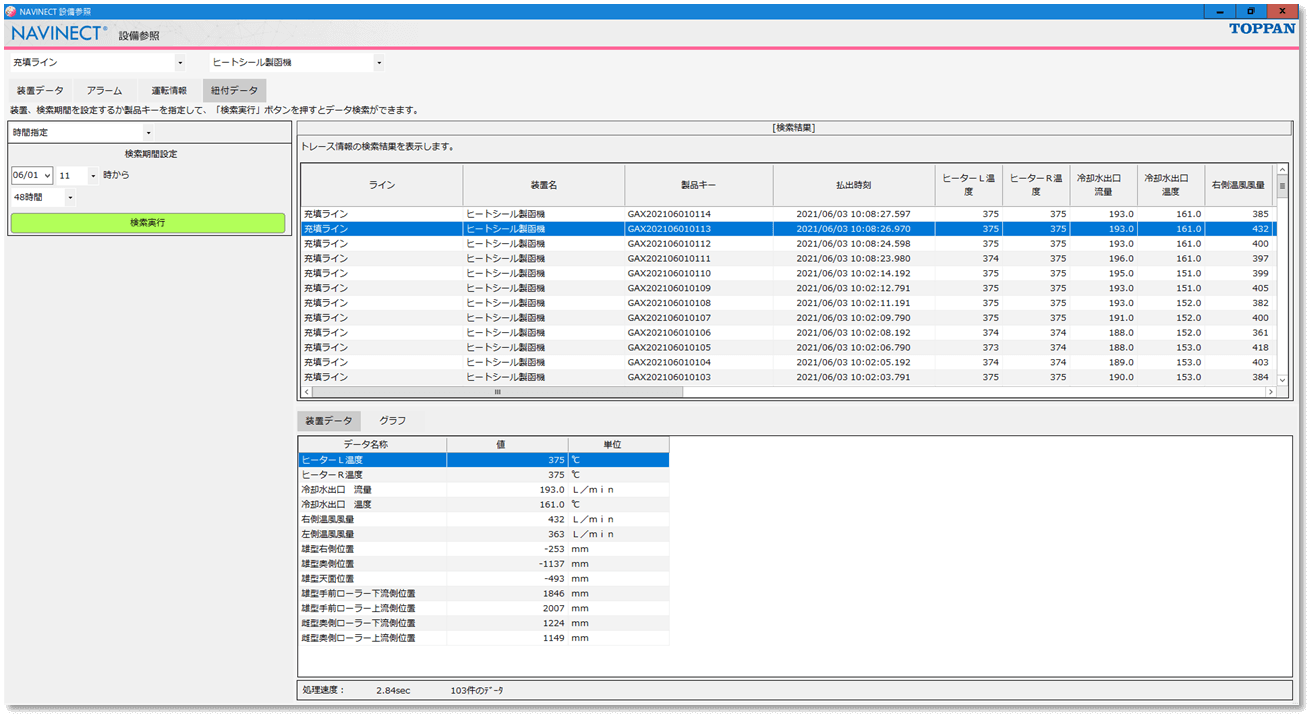
製造現場におけるトレーサビリティ導入のメリット
トレーサビリティは、企業が製品に関する社会的責任を果たすための仕組みであると同時に、サプライチェーンを構成する個々のステークホルダーに対し以下のようなメリットをもたらす仕組みでもあります。
-
不良品回収範囲の極小化
不良品の個体IDが明確になることで、生産設備などの異常発生期間中に完成した製品を的確に割り出すことが可能となります。
-
不要なコスト発生の防止
不良品回収範囲が明確になることで、良品を不良品として回収してしまうリスクを低減することに繋がり、余分な回収 / 廃棄コストや製品ロスの発生を防ぎます。
-
顧客満足度の向上
客観的な製造過程の情報が蓄積され遡及可能となることは、製造データの改ざんなどの不正防止に繋がり、取引先やエンドユーザーへ安心を提供します。 またクレームが発生した際に、正確で迅速な原因究明が可能となることで顧客の信頼回復を早めます。
トレーサビリティの実現は、リスク対策・業務効率・品質など多方面で、企業・取引先・エンドユーザーに広く恩恵をもたらすものです。このようなメリットの豊富さと冒頭述べたサプライチェーン全体でのトレーサビリティ実現の必要性から、製造を担う企業だけでなく流通などの製造を取り巻く幅広いステークホルダーが、上記メリットを最大化できる形でトレーサビリティを実現させようとしています。
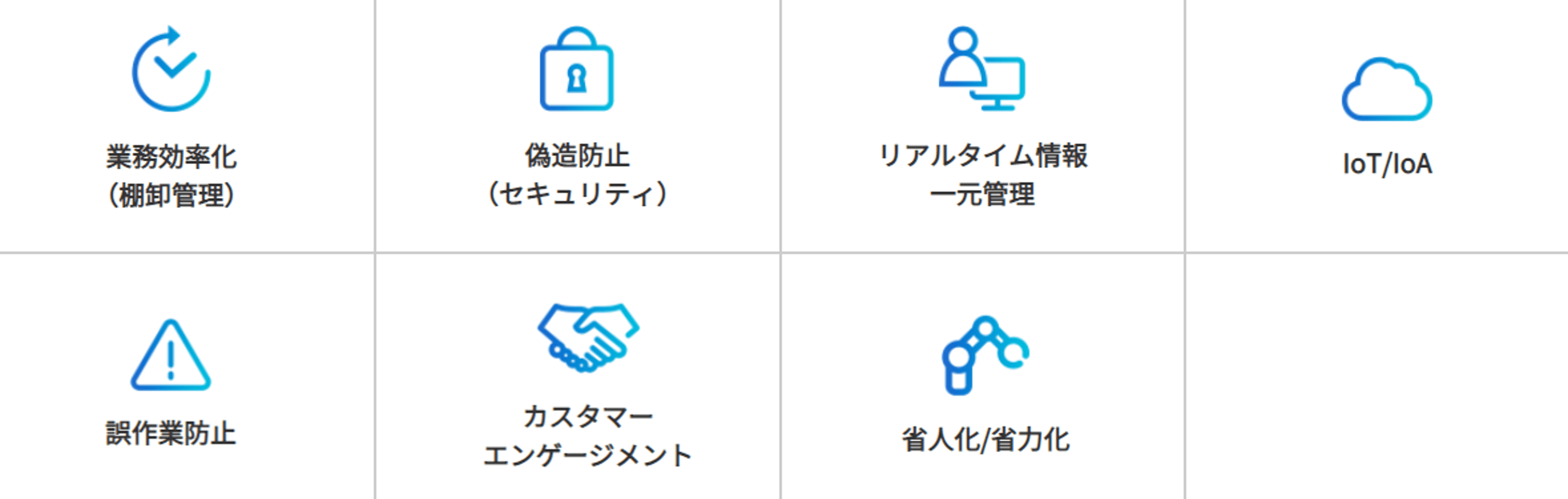
トレーサビリティの実現により製造品質の向上へ
トレーサビリティの実現には、「原材料や製品の状態に応じた個体ID付与方法」「工程環境に適したID読取り用のリーダー」「操作性 / 視認性に優れた管理システム」の3点を選定する必要があります。 取り扱う製品や製造現場の環境に適した運用を検討する必要があるため、導入に際しては現場の課題ヒヤリング・製造現場の環境調査・機器の手配やシステム設定など複数のステップを踏みます。 運用のコンサルティングから必須アイテムの導入までを一気通貫に実施できるパートナー(ベンダー)を見つけることが、最小限の負荷でトレーサビリティの導入効果を最大化することに繋がります。 また、トレーサビリティそのものの実現に加えてSPCのような、生産設備や工程の環境をデジタルデータで管理できる仕組みが導入されていると、より盤石な品質管理体制が構築可能となります。
終わりに
「製造業におけるデータインテグリティとは【各論編②】」でご紹介したSPCに続き、昨今のトレンドワード「トレーサビリティ」についてご紹介しました。 SPCとトレーサビリティどちらを実現する上でも重要となるポイントとして、生産設備・工程の環境・製品に関するデータがデジタルで管理されていることが挙がります。どちらも、製造現場や製品の品質を維持・向上させる上で最適の手段ですが、各種データが客観的なデジタルという形式で管理され、容易に遡及可能である必要があります。 一方、今まで紙などでデータを管理していたアナログな製造現場においては、デジタルデータを前提としたSPCやトレーサビリティの導入はかえって製造現場の負荷を増大させたり、慣れないシステムによる運用の非効率さを生じさせる原因ともなりかねません。 製造現場のデジタル化を実現するには、情報共有や確認作業のペーパーレス化をファーストステップとし、設備データの統合管理・統合データのリモート監視・遠隔からの多拠点設備制御…といったように、段階的なステップアップを踏む必要となります。
データインテグリティを向上させる
NAVINECTエッジ「品質管理」パッケージを見る >>
生産装置の稼働情報をリアルタイムに監視する
NANINECTエッジ「生産監視」パッケージを見る >>
NAVINECTではその他にも製造DXに役立つさまざまな機能をラインナップしています。是非お気軽にお問い合わせください。
関連記事
-
NAVINECTの特徴を知る
-
NAVINECT製品を知る